Bei der Automatisierung von LNG-Anlagen sowie Schiffen zum LNG Transport aber auch mit LNG-Antrieb bringen Remote I/O-Systeme viele Vorteile. Sie sparen Platz und Gewicht und eröffnen bessere Bedienmöglichkeiten. Neuste technische Entwicklungen wie Ethernet-APL ebnen nun den Weg ins digitale Zeitalter.
Der globale Bedarf nach LNG wächst nahezu ungebremst. Bis 2040 muss eine Versorgungslücke von rund 390 Millionen Tonnen pro Jahr geschlossen werden. In den nächsten Jahren werden daher zahlreiche weitere Anlagen zur Verflüssigung von Erdgas entstehen. Weltweit werden zudem die sich daran anschließenden Wertschöpfungsketten – von Beladungsvorrichtungen über Tanker bis hin zu Entladeterminals und Regasifizierungsanlagen – ausgebaut. Schon heute rüstet R. STAHL rund 80 Prozent der LNG-Tanker mit seinen Produkten aus. Insbesondere auch Remote-IO-Systeme kommen dort zum Einsatz.
Höchste Anforderungen an den Ex-Schutz
Selbst wenn die Zahl der LNG-Unfälle in der Vergangenheit gering war, verdeutlichen Vorkommnisse wie bei Freeport in Texas (USA) oder in Hammerfest (Norwegen): Bei der Ausrüstung von LNG-Anlagen sind einwandfrei funktionierende Sicherheitseinrichtungen das A und O. Auch gilt es, alles zu tun, damit menschliches Versagen so unwahrscheinlich wie nur möglich wird. Bei sachgemäßem Aufbau und Betrieb sind die Gefahren von LNG-Anlagen jedoch genauso gut beherrschbar wie bei anderen Prozessanlagen.
LNG, das weitgehend aus Methan besteht, gehört zur Explosionsgruppe IIA und zur Temperaturklasse T1. Es ist damit zwar weniger explosionsgefährlich als Wasserstoff (IIC) – dennoch gilt es, die Explosionsgrenzen (UEG 4,4 Vol.%, OEG 17,0 Vol.%) und weitere sicherheitstechnische Kennwerte zu beachten. Die Energieversorgung von LNG-Anlagen ist mit explosionsgeschützten Produkten, die zahlreich zur Verfügung stehen, zu gewährleisten. Auch für Prozessinstrumentierung und lokale Bedienung stehen geeignete Geräte bereit. Beleuchtung, Überwachung & Security sind ebenfalls mit Hilfe von Ex-zertifiziertem Equipment umzusetzen. R. STAHL bietet für alle diese Anwendungen in LNG-Applikationen geeignete Produkte. Einen besonders hohen Stellenwert haben die Automatisierung sowie die Digitalisierung als Schlüssel für zukunftsfähige Installationen. Denn wer LNG effizient produzieren und transportieren und damit zu wettbewerbsfähigen Preisen anbieten will, der sollte auch auf eine möglichst effiziente Automatisierung der Anlagen achten.
Mit modernen HMI-Systemen Bedienfehler minimieren
Bedien- und Beobachtungssysteme, die für den Ex-Bereich ertüchtigt sind, unterstützen Anwender dabei, Fehler zu vermeiden. Moderne HMI-Systeme leisten dies deutlich effektiver als früher übliche Drucktaster und Leuchtmelder. Sie geben eindeutige Hinweise auf Handlungsoptionen und reduzieren somit menschliche Fehler. Auch im Sektor Security sind in der letzten Zeit etliche Neuerungen für den Ex-Bereich entstanden. Vermehrt werden in LNG-Anlagen zur Produktion oder Verflüssigung Kameras und CCTV-Equipment eingesetzt, um sie vor unbefugten Eingriffen zu schützen.
Remote-I/O-Technologie als Basis für digitale Konzepte
Besonders große Fortschritte haben sich in den zurückliegenden Jahren im Sektor Digitalisierung ergeben. Remote I/O-Technologie realisiert dabei die digitale Datenübertragung und eröffnet umfangreiche Diagnosemöglichkeiten. Zudem können damit die neusten Automatisierungskonzepte wie etwa NOA (NAMUR Open Architecture) verwirklicht werden. Insbesondere dank der Entwicklung von Ethernet-APL, durch welches Ethernet im Feld zukünftig auch in explosionsgefährdeten Bereichen Realität wird, können LNG-Anlagen noch mehr davon profitieren.
Moderne Remote I/O-Systeme unterstützen zudem Strukturen wie sie von OPAF (Open Process Automation Forum) konzipiert wurden, um Anlagen mit lokalen Kleinintelligenzen auszurüsten. Auch für modulare Anlagen nach dem MTP-Standard (Module Type Packaging) bringen erste Remote I/O-Systeme das nötige Rüstzeug mit. Sogar in der installierten Basis lassen sich diese innovativen Konzepte verwirklichen und so zusätzliche Effizienzpotenziale erschließen.
Remote I/O-Systeme für Zone 1 von R. STAHL sind so ausgelegt, dass sie weltweit einsetzbar sind. Sie verfügen über die notwendigen Zertifizierungen für Gas- und Staub-Ex-Atmosphären – angefangen von ATEX und IECEx über FM für die USA sowie Kanada, EAC für Russland, INMETRO für Brasilien; PESO für Indien sowie KTL für Korea usw. Für den Bau von LNG-Tankern sowie Schiffen, die mit Hilfe von FGSS mit LNG angetrieben werden, liegen zudem zahlreiche Zulassungen vor (DNV, LR, BV, ABS, CCS, KRS, ClassNK, PRS, RINA, RS, …).
CAPEX- und OPEX-Einsparungen
Im Vergleich zu konventionellen Installationen spart die Remote I/O-Technik erhebliche Mengen an Schränken und Kabeln ein. Eine typische Installation, die bislang zehn Schränke benötigte, reduziert sich auf zwei bis drei Schränke. Mit Buskabeln lassen sich weite Entfernungen kostengünstig überbrücken; die Feldgeräte werden im Feld über intelligente Verteiler angeschlossen. Je nach Installation reduziert die Remote I/O-Technik die CAPEX-Kosten um 25 bis 47 Prozent. Durch schnellere Produktionsstarts und höhere Verfügbarkeit, die auf integrierte Diagnosen und Alarme zurückzuführen ist, können zudem OPEX-Einsparungen realisiert werden. Ihre Höhe ist schwer zu beziffern. Ein einziger Stillstand, der vermieden werden kann, ist bei einer LNG-Anlage von unschätzbarem Wert. Erweiterte Diagnosemöglichkeiten erhöhen zudem die Prozess- und Produktqualität.
Leichteres Gewicht, mehr digitale Intelligenz an Bord von LNG-angetriebenen (Kreuzfahrt)-Schiffen
Weniger Schränke und Einsparungen bei der Verdrahtung bedeuten darüber hinaus auch erhebliche Gewichtseinsparungen. Bei einem realen Projekt mit um die 1000 Signalen ergibt sich durch die Remote I/O-Installation eine Einsparung von mehr als 80 Prozent Gewicht – von 23-28 Tonnen auf lediglich 3,8 Tonnen, wobei Redundanz- und Reserve-Konzepte umgesetzt wurden.
Auch in FGSS (Fuel Gas Supply Systems) für den Antrieb von LNG-Tankern, aber zunehmend auch anderen Schiffen wie etwa Kreuzfahrtschiffen, macht sich die Gewichtseinsparung sowie die kompakte Bauweise bezahlt. Zudem sind auf Schiffen häufig nur wenige technische Spezialisten an Bord. In Verbindung mit modernen Bediensystemen ermöglicht die Remote I/O-Technik die vereinfachte Bedienung und Fehlersuche. Sogar Remote-Zugänge für externe Spezialisten lassen sich realisieren.
Wählen Sie mit Remote I/O Ihr Wunsch-Protokoll!
Moderne Remote I/O-Lösungen in Zone 1 unterstützen zahlreiche Protokolle – neben Profibus DP inzwischen auch Profinet, EtherNet/IP, Modbus TCP etc. Diverse OT/IT-Applikationen sind über die offene Diagnose-Schnittstelle machbar, und zwar nicht nur über HART, dem „Großvater“ im Asset Management-Bereich. Auch moderne Konzepte über FDT/DTM oder OPC UA sowie zukünftig mit FDI lassen sich verwirklichen. Besonders hilfreiche Web-Server-Technologien unterstützen so nachhaltig bei der Fehlersuche.
NOA, OPA und UniversalAutomation.org einfach umsetzen
Das bereits erwähnte NOA-Konzept, das einen zweiten Kanal für Monitoring & Optimization-Kanäle eröffnet, lässt die einfache Erschließung von Zusatzdiagnosewerten zu, ohne dass der Hauptprozess beeinträchtigt werden kann. Ebenfalls relativ neu ist das Konzept der UniversalAutomation.org. Es arbeitet mit dem offenem ecoRT Runtime (nach IEC 61499), öffnet also die sonst geschlossene Leitsystemwelt für I/O-Systeme und Package Units, die über offene Runtimes mit dem Leitsystem kommunizieren können. Wer sich mit dem IEC 61499-Standard näher beschäftigt, wird schnell feststellen, dass sich aus der Interoperabilität, die Kopplungs- und Anpassungsarbeiten überflüssig macht, viele Vorteile ergeben. R. STAHL ist Gründungsmitglied der UniversalAutomation.org und unterstützt bei der Verbreitung der Technologie.
Innovative Automatisierungsstrukturen hat auch das OPA Forum, getrieben u. a. von Exxon Mobile, entwickelt. Dabei kommunizieren kleine intelligente I/O-Systeme, die mit der R. STAHL-Remote I/O-Hardware im Zusammenspiel mit Steuerungstools auf Basis von IEC 61499 und IEC 61131 (z.B. CoDeSys) umgesetzt werden können.
Modularer Anlagenbau leicht gemacht
Für zahlreiche Anwendungen in der LNG-Wertschöpfungskette kommen modulare Anlagenkonzepte zum Einsatz, bei welchen fertig automatisierte Package Units in die Gesamtanlagenstruktur eingebunden werden. Am reibungslosesten funktioniert dies über standardisierte MTP-Schnittstellen. Auch dies lässt sich mittels Remote I/O-Technik in Verbindung mit MTP-Bibliotheken und z.B. einer IEC 61131 basierten Runtime realisieren. So entstehen außerordentlich flexible Digitalisierungsplattformen für die LNG-Wertschöpfungskette.
Endlich durchgängig Ethernet bis in den Ex-Bereich
Auch im Bereich Netzwerk gibt es inzwischen Technologien, die das Thema Explosionsschutz und Innovation unter einen Hut bringen. Schon lange gilt Ethernet als „DIE“ Technologie, um die Vernetzung durchgängig über alle Ebenen der Prozessautomation aufzubauen. Um dies auch im Ex-Bereich umzusetzen, existieren einige wenige Lösungen, unter welchen Ethernet-APL als innovativste und interessanteste gilt. Sie wird von den vier großen Feldbusorganisationen Profibus+Profinet International, FieldComm Group, ODVA und OPC Foundation sowie zahlreichen Herstellern von Leitsystemen, Feldgeräten und Ex-Schutz-Technologie unterstützt.
Es würde an dieser Stelle den Rahmen sprengen, auf alle Details einzugehen. Zu den technischen Eckdaten gehört, dass die Technologie eine Ethernet-Übertragung mit 10 Mbit/s mittels 2-Draht-Kabel über Distanzen von 1000 Meter unterstützt. Sie ist also auch für sehr große Anlagen geeignet. Der Explosionsschutz ist integriert; Feldgeräte in Zone 1 werden eigensicher mit Energie versorgt. Ethernet-APL unterstützt alle Ethernet-Protokolle inklusive PROFINET, EtherNet/IP und OPC UA sowie HART-IP.
Ethernet-APL versorgt Feldgeräte eigensicher mit Energie
Explosionsschutz ist integriert. Das geht so weit, dass die Feldgeräte, die in der Zone 1 installiert sind, eigensicher mit Energie versorgt werden, sodass kein separates Energie-Netzwerk benötigt wird. Das spart Kosten. Zudem bieten die Ethernet-APL Field Switches dem Betreiber zusätzliche Möglichkeiten. Sie sind vollgepackt mit Diagnosefunktionen, sodass die Anlage, sowohl die Physical Layers als auch die Netzwerke, sehr einfach an zentraler Stelle analysiert werden kann.
Fazit: LNG-Anlagen durchgängig automatisiert und digitalisiert
Gerade für Anlagen im Sektor LNG, die sich derzeit in Planung befinden, ist die Ethernet-APL-Technologie sehr gewinnbringend einsetzbar. Es entstehen durchgängige Lösungen, die auf keinen Fall komplizierter als herkömmliche Installationen sind. Die digitalen Produkte und Systeme führen vielmehr zu deutlichen Erleichterungen. Produkte werden Mitte 2023 verfügbar sein, darunter auch ein Ethernet-APL-FieldSwitch von R. STAHL. In Kombination mit den modernen Automatisierungsstrukturen, die sich mithilfe von Remote I/O-Technik verwirklichen lassen, entstehen so LNG-Anlagen, die sich mit Sicherheit als zukunftsfähig und auf lange Sicht äußerst effizient erweisen werden.
Weiterführende Links:
Diese beiträge könnten Sie auch interessieren
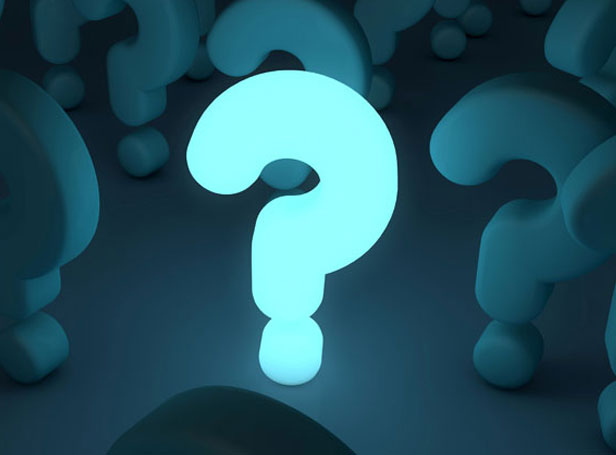
Ethernet-APL und funktionale Sicherheit – geht das?
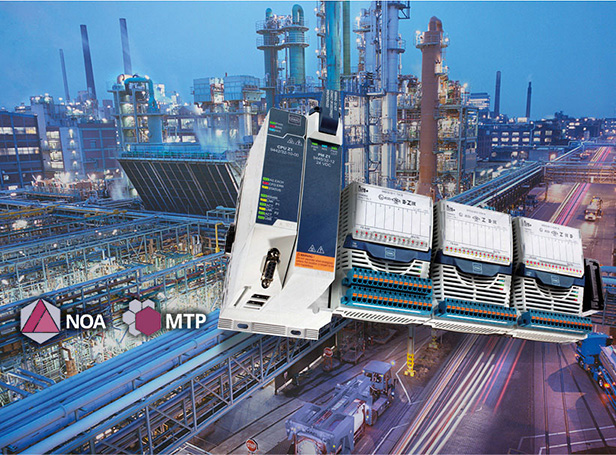
Lokale Intelligenz für die Prozessautomatisierung
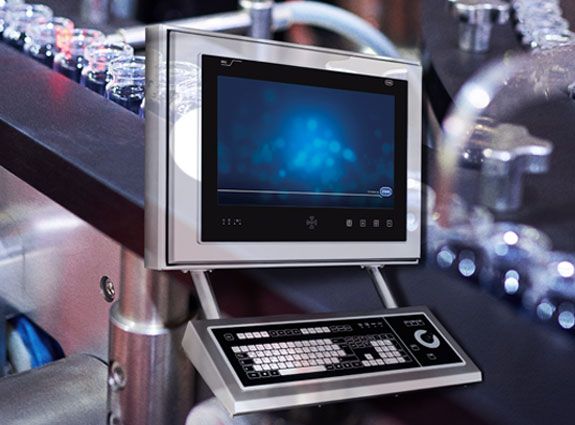
Neuen Kommentar schreiben