„Eine hochwertige Datenbasis ist die Grundlage für eine erfolgreiche Digitalisierung“
Mit der neuen Digital Twin-Plattform für digitale Typenschilder liefert R. STAHL ein Musterbeispiel, wie Verwaltungsschalen genutzt werden können, um bei der Planung und dem Betrieb von Geräten in der Prozessindustrie Nutzen zu schaffen. Für welche Anwender das besonders vorteilhaft ist, erläutert Roland Dunker im Interview.
1. Herr Dunker, was waren die grundlegenden Überlegungen und Beweggründe für die Entwicklung Ihrer neuen Plattform?
Die Motivation war, eine Plattform zu schaffen, die ausschließlich für Anwender von Verwaltungsschalen konzipiert ist. Wir wollten eine Lösung bieten, die unabhängig von Download-Bereichen oder Standardplattformen agiert. Unsere Plattform ist darauf ausgelegt, die verschiedenen Bedürfnisse der Nutzer zu adressieren – von Anfängern bis hin zu erfahrenen Planern.
2. Wie haben Sie die Bedürfnisse der verschiedenen Nutzergruppen berücksichtigt?
Wir haben intensiv darüber nachgedacht, wo Daten entstehen – vollkommen losgelöst davon, in welchem System und mit welchen Methoden sie erfasst, gespeichert oder verteilt werden und wie die Zugriffsrechte sind. Wir haben einfach nur betrachtet, wo sie entstehen, wie sie genutzt werden und was man damit machen kann. Aus diesen Use Cases haben wir dann überlegt, was mit einem digitalen Zwilling verknüpft werden sollte, sodass der größtmögliche Nutzen für den Anwender entsteht. Dabei sind sechs Use Cases entstanden – und die Diskussionen der letzten zwei Jahre haben gezeigt, dass wir damit genau den Nerv der Industrie getroffen haben.
3. Wie war das Feedback auf der ACHEMA?
Die Kunden haben uns bestätigt, dass dies die relevanten Anforderungen sind. Es wird klar gesagt, dass durchgängige Informationen gebraucht werden, die nicht zunächst aus einem PDF kopiert werden müssen. Die Datenketten müssen durchgängig sein. Weil der Lebenszyklus bislang nicht abgebildet werden kann, sind auch die Daten in Engineering-Plattformen meist nicht aktuell. Im Feld braucht man direkt Zugriff auf die richtigen Dokumente und Informationen, nicht auf 300-seitige PDFs. Man muss wissen, welche Nachfolgeprodukte es gibt, weil das Stillstandszeiten beeinflusst. Die Industrie braucht diese Informationen, und genau da entsteht Mehrwert, indem wir die Daten verknüpfen. Auch das Thema Firmwareupdates für smarte Produkte ist wichtig. Firmen bestätigen, dass sie auf Sicherheitslücken prüfen müssen, aber keine Ressourcen dafür haben. Zudem sehen sich Betreiber einer wachsenden Regulatorik gegenüber – es muss immer mehr dokumentiert werden und versionierte Dokumente sollen griffbereit sein. Gleichzeitig haben sie immer weniger Personal. Deshalb sind unsere Kunden für jede digitale Lösung dankbar, die das Leben einfacher macht.
4. Ihre Plattform berücksichtigt lediglich Geräte von R. STAHL, in einem Betrieb werden aber auch viele Geräte anderer Hersteller eingesetzt. Rechtfertigt das die Nutzung Ihrer Plattform trotzdem?
Ja. Auch wenn nur ein Produkt mit einer Verwaltungsschale ausgestattet ist, hat ein Servicetechniker einen großen Nutzen. Wartungsinformationen kommen oft aus PDF-Dokumenten – aber die Daten haben auch eine Lebensgeschichte. Wir publizieren die Daten zur Wartung und übergeben sie in der PDF, wenn es keine Verwaltungsschale gibt. Der Anlagenbauer muss alle Wartungsinformationen rauskopieren, ergänzt diese mit eigenen Anweisungen und übergibt das dann an den Betreiber, der alles manuell in seine Service-Software überträgt. Das ist ein großer Aufwand. Mit unserer IEC 61406-konformen Lösung kann der Techniker einfach das Typenschild scannen und so das Asset in der Service-Software identifizieren. Er hat eine saubere Datenbasis, muss keine separaten Tags vergeben und kommt direkt an die Informationen.
Wir zeigen, wie einfach die Integration ist, und das ist ein Differenzierungsmerkmal. Bei vergleichbaren Produkten ist der Integrationsaufwand ein wichtiges Entscheidungskriterium. Bietet ein Gerätehersteller nur ein Datenblatt, dann ist der Integrationsaufwand groß. Vielen Prozessbetreibern wird bewusst, dass mit der Verwaltungsschale ein industrieübergreifender Standard etabliert wird, der genau diese Probleme löst.
5. Es ist also ein Differenzierungsmerkmal, das dazu führt, dass Produkte von R. STAHL bevorzugt werden?
Definitv! Die Möglichkeit, im Feld einfach zu scannen und direkt auf alle Daten und Dokumente zuzugreifen, den Wartungsstatus vor Ort zu kennen und im Servicefall Nachfolgeprodukte zu sehen, begeistert die Kunden. So positionieren wir uns als Technologieführer. Und damit erfüllen wir sogar schon Teile der Anforderungen aus der künftigen Ecodesign for Sustainable Products Regulation, ESPR.
6. Welche Herausforderungen sehen Sie bei der Umsetzung der EU-Regulierungen zum digitalen Produktpass?
Die größte Herausforderung ist in vielen Unternehmen die Qualität der Stammdaten. Diese sind historisch gewachsen und oft nicht gut gepflegt. Eine einheitliche und qualitativ hochwertige Datenbasis ist aber die Grundlage für eine erfolgreiche Digitalisierung. Wenn diese einmal steht, ist die Transformation zur Verwaltungsschale oder anderen Formaten ein relativ kleiner Schritt. Unternehmen müssen jetzt ihre Hausaufgaben machen und in die Datenqualität investieren.
7. Was müssen die Hersteller und Betreiber jetzt konkret tun, um sich auf die kommenden Anforderungen vorzubereiten?
Hersteller und Importeure müssen bis 2026 sicherstellen, dass ihre Produkte einen digitalen Produktpass haben. Betreiber werden in der Folge ebenfalls die Vorteile der Digitalisierung erkennen und ihre bestehenden Anlagen nachrüsten. In beiden Fällen ist der erste Schritt eine umfassende Datenbereinigung und -standardisierung, um die Voraussetzungen für die Verwaltungsschalen zu schaffen.
8. Können Sie die wirtschaftlichen Vorteile im Engineering-Prozess quantifizieren?
Nehmen wir ein Beispiel aus dem Pharmabereich: Dort wissen wir von einem Unternehmen, das Bioreaktoren entwickelt, dass dieser Anlagenbauer durch das komplett digitale Engineering deutlich schneller entwickeln kann. Der Planungsprozess ist normalerweise sequentiell, aber durch die parallele Arbeit mit Simulations- und 3D-Modellen konnten mehrere Jahre Entwicklungszeit eingespart werden. Das ist unbezahlbar.
Beim Einpflegen von Gerätedaten in Engineering-Tools sparen Techniker und Ingenieure im Durchschnitt rund eine Stunde pro Asset.
9. Gibt es schon Pläne für die zukünftige Entwicklung der Plattform?
Wir haben eine komplette Roadmap mit verschiedenen Use Cases. Zum einen werden wir Suchmodelle erweitern, die Produkt- und Engineering-Aspekte abdecken. Wir haben drei Komplexitätsstufen bei unseren Produkten: Komponenten, konfigurierbare Produkte und Einzelengineering. Wir bauen individuelle Lösungen für Kunden und integrieren Daten von Zulieferern. Langfristig werden wir die Anforderungen des digitalen Produktpasses erfüllen und alle geforderten Daten zur Verfügung stellen.
Weiterführende Links:
Diese beiträge könnten Sie auch interessieren
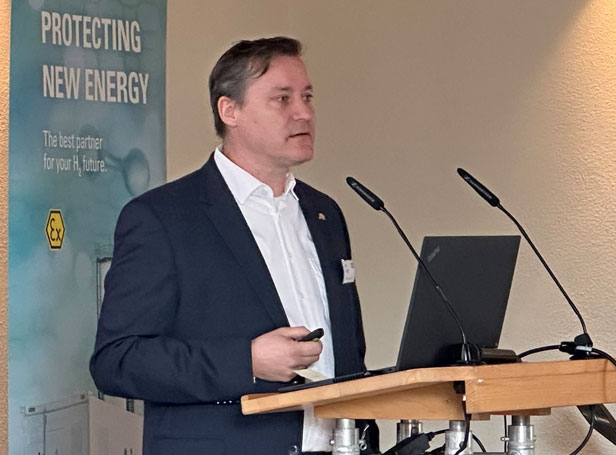
Neuen Kommentar schreiben