Die Reinraumtechnik ist in der Industrie häufig anzutreffen. So treten beispielsweise bei der Produktion, Verarbeitung sowie Montage von Elektronik, Feinwerktechnik und Optik oder in der Pharmazie, Biotechnologie, der Nahrungsmittelherstellung sehr hohe Anforderungen an die Technik und die Luftreinheit auf. Nur durch die Einhaltung festgelegter Reinheitsgrade der Luft am Arbeitsplatz kann die Qualität der Produkte und häufig auch die Gesundheit der Mitarbeiter sicher gewährleistet werden.
Häufig hat man es bei diesen Prozessen auch mit brennbaren Substanzen in Form von Flüssigkeiten oder Stäuben zu tun. Im ungestörten Zustand befinden sich diese natürlich in geschlossenen Apparaturen. Im Störfall kann es aber zu einer Freisetzung und dadurch zur Bildung einer explosionsfähigen Atmosphäre kommen. Auch während der Reinigung mit brennbaren Lösungsmitteln kann Explosionsgefahr entstehen. Daher müssen auch in Reinräumen die Anforderungen des Explosionsschutzes erfüllt werden. Wie dies geschieht wird im folgenden Beitrag beschrieben.
Überblick über die Reinraumtechnik
Allgemein gesprochen hat die Reinraumtechnik die Aufgabe, bestimmte Arbeitsbereiche vor unerwünschten äußeren Einflüssen zu schützen. Die äußeren Einflüsse treten in Form von Verunreinigungen auf, die sowohl gasförmig sein können als auch als feste oder flüssige Partikel unterschiedlicher Größe vorkommen. Die schädliche Wirkung dieser Partikel kann auf unterschiedliche Weise erfolgen:
- Die zunehmende Miniaturisierung, die ihre deutlichsten Ausprägungen in der Mikroelektronik und der Mikrostrukturtechnik findet, führt dazu, dass selbst kleinste Mengen prozessfremder winziger Partikel zu einer nachhaltigen Beeinträchtigung der Produktqualität führen können. Verständlich wird diese Tatsache, wenn man die heute typischen Strukturgrößen in der Mikroelektronik betrachtet, die sich im Submikrometerbereich bewegen und diese Dimensionen mit der durchschnittlichen Korngröße von Hausstaub vergleicht, die um Größenordnungen darüber liegt.
- Die Fertigung vieler pharmazeutischer Produkte verlangen nach einem sehr hohen Grad an Asepsis. Keime, Staub und insbesondere Mikroorganismen wirken sich negativ auf die Qualität der Präparate aus und können unter Umständen auch zu gesundheitsschädlichen Nebenwirkungen führen.
- Viele der in der Pharmazie verwendeten Wirkstoffe sind hochaktiv und giftig. Selbst der Kontakt mit kleinsten Mengen dieser Subtanzen kann zu schweren Schädigungen der in der Fertigung Beschäftigten führen.
Allgemein gesprochen geht es also in der Reinraumtechnik zum einen um den Schutz von Produkten, Betriebsmittel und Fertigungsprozessen vor verunreinigungs-bedingten Schäden oder Leistungseinbußen – und zum anderen um den Schutz der in den Fertigungsprozessen tätigen Personen vor gesundheitsschädigenden Prozessrisiken. Dies erfolgt durch die Bereitstellung von Arbeitsumgebungen mit einer genau spezifizierten Luftreinheit in Bezug auf luftgetragenen partikelförmiger Fremdstoffe.
Bei der Planung und Errichtung von Reinräumen ist eine enge Zusammenarbeit zwischen dem späteren Nutzer und dem Errichter der Anlage erforderlich um die notwendigen Reinheitsanforderungen mit einem vertretbaren finanziellen Aufwand zu erfüllen. Die realisierte Lösung muss optimal an den jeweiligen Anwendungsfall angepasst werden. Wichtige Eingangsgrößen sind dabei verschiedene Prozessparameter, wie die Anzahl der gleichzeitig tätigen Personen, die Notwendigkeit von Schutzausrüstungen, die Wärmeentwicklung, die zu verarbeitenden Substanzen, die erforderliche Reinheit ausgedrückt in Reinheitsklassen, die Installationsdichte und die Gebäudestruktur. Häufig sind auch noch verschiedene behördliche Auflagen zu erfüllen.
Die enge Verbindung der Gestaltung des Reinraumes mit dem jeweiligen Anwendungsfall mag ein Grund dafür sein, dass die Landschaft der internationalen und nationalen Normen und Richtlinien zum Thema Reinraum lange Zeit sehr heterogen und lückenhaft war. Erst seit einigen Jahren gibt hier eine spürbare Entwicklung, die es dem Hersteller von Equipment für Reinräume erlaubt, standardisierte Produkte für verschiedene Anwendungsfälle zu liefern.
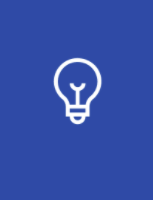
Um später im Betrieb eine sichere Chargenproduktion gewährleisten zu können, muss die kontinuierliche Erfassung und Dokumentation aller kritischen Reinraumparameter, nämlich Temperatur, Luftfeuchte, Druckdifferenz und Partikelzahl gewährleistet sein. Ausgehend von den zunehmend strengeren Anforderungen an die Umgebungsbedingungen bei der Herstellung und Abfüllung von Arzneimitteln durch internationale und nationale Behörden wie der WHO, der EU oder der US-amerikanischen FDA, kommt der kontinuierlichen Überwachung der Umgebungsbedingungen sowie der lückenlosen Dokumentation der dabei erfassten Daten ein stark gewachsener Stellenwert zu.
Explosionsschutz in Reinräumen
Die in Reinräumen verarbeiteten Substanzen und Wirkstoffe sind sowohl als Stäube als auch als Flüssigkeiten sehr häufig brennbar und können so zusammen mit dem Luftsauerstoff eine gefährliche explosionsfähige Atmosphäre bilden. Wegen der besonderen Anforderungen an die Umgebungsbedingungen finden die meisten Prozesse zwar in geschlossenen Apparaturen statt, aber es können auch Prozessschritte wie beispielweise das Abfüllen staubförmiger Substanzen oder Flüssigkeiten vorliegen, bei denen brennbare Stoffe in kleinen Mengen außerhalb geschlossener Behälter gehandhabt werden. Weiterhin müssen bei der Ermittlung des Explosionsrisikos auch verschiedene Anlagenzustände berücksichtigt werden, bei denen keine Reinraumbedingungen herrschen, aber eine Explosionsgefahr vorliegen kann. Solche Anlagenzustände sind beispielsweise Probeläufe, das Anfahren einer Anlage sowie Prüf- und Wartungsprozeduren.
Eine Besonderheit stellen Reinigungsprozesse dar. Häufig müssen zur gründlichen Reinigung der Räume und Apparaturen Lösungsmittel verwendet werden. Selbst wenn im Prozess keine brennbaren Substanzen verwendet werden, zwingt dies zur Einstufung in einen explosionsgefährdeten Bereich.
Die Einstufung der explosionsgefährdeten Reinräume selbst richtet sich nach der Art der verwendeten brennbaren Substanzen und nach der Häufigkeit des Auftretens einer explosionsfähigen Atmosphäre.
Beispiel einer Reinraumanlage mit explosionsgefährdeten Bereichen
Im Folgenden sollen die Explosionsschutzmaßnahmen in Reinräumen anhand einer Anlage eines großen Pharmaherstellers erläutert werden: Die hohen Reinheitsanforderungen sind zum einen prozessbedingt und zum anderen aufgrund der Anwesenheit einiger hoch reaktiver Stoffe erforderlich. Die Anlage wurde innerhalb von drei Jahren geplant und in einem bereits bestehenden Gebäude über mehrere Etagen errichtet. Da für die regelmäßige Reinigung der Räume brennbare Lösungsmittel verwendet werden, müssen die erforderlichen Maßnahmen des Explosionsschutzes getroffen werden.
In der obersten Etage befinden sich die sogenannten Reaktorräume. Der Begriff ist etwas irreführend, denn die großen Reaktoren sind senkrecht über mehrere Etagen in das Gebäude eingebaut und in diesen Räumen befindet sich lediglich der obere Reaktorbereich. Wegen der überwiegend geschlossenen Prozesse liegen keine besonderen Anforderungen an die maximal zulässige Partikelkonzentration in den Räumen vor, dafür aber für die Reinigung des Raumes und der Ausrüstung. Aus Gründen des Personenschutzes müssen Kontaminierungen einfach und gründlich zu entfernen sein.
Die Automatisierungstechnik der Anlage basiert auf untereinander vernetzten Remote-PCs, welche keine Anbindung an ein übergeordnetes Prozessleitsystem haben und einem für die Zone 1 geeigneten Feldbussystem (Profibus PA), welches die kommunikationsfähigen Sensoren und Aktoren vernetzt. Über die Remote-PCs werden die Prozesse im jeweiligen Raum direkt gesteuert. Eine Fernsteuerung aus einem anderen Raum ist nicht möglich – lediglich sicherheitskritische Befehle können zu einem anderen PC übertragen werden.
Eine Etage tiefer befindet sich der Mischungsraum. Hier erfolgt die sogenannte Vordetaillierung der Substanzen. Das heißt: es werden hier pastöse Substanzen durch Mischung verschiedener Ausgangsstoffe unter Verwendung von Lösungsmittel hergestellt. Da hier ein überwiegend offenes Handling der Ausgangsstoffe stattfindet, werden strengere Anforderungen an die Prozessreinheit gestellt, und es darf deshalb eine maximale Verunreinigung von 100.000 Partikeln pro Kubikfuß nicht überschritten werden.
Sämtliche Wände sind in Edelstahl ausgeführt und so gestaltet, dass sich keine Staubablagerungen bilden können, bzw. dass ein Reinigen leicht möglich ist. Der Fußboden wurde mehrfach geschliffen und lackiert. Zur Beleuchtung dienen explosionsgeschützte Edelstahl-Deckeneinbauleuchten der Gerätekategorie 2. Aufgrund der besonderen Arbeitsanforderungen wird hier eine hohe Beleuchtungsstärke verlangt. Sowohl der Mischungs- als auch der Reaktorraum dürfen aus Personenschutzgründen nur in einem fremdbelüfteten Schutzanzug über eine Schleuse betreten werden. Auch hier sind die oben erwähnten Deckeneinbauleuchten installiert.
In der gesamten Anlage wird auf eine strikte Trennung des Personenverkehrs vom Materialtransport Wert gelegt. Deswegen befinden sich neben den Schleusen für das Personal separate Schleusen für das Material.
Im Erdgeschoss befindet sich der untere Teil des Reaktors. Hier erfolgt die Entnahme und Weiterbehandlung der Reaktionsprodukte mit Zentrifugen und verschiedenen Trocknungseinrichtungen.
Im Kellergeschoss sind verschiedene Kessel angeordnet, die zum einen zur Sammlung des Abwassers dienen und zum anderen Sicherheitsfunktionen erfüllen. Bei einer Notabschaltung der Anlage wird die gesamte Reaktorflüssigkeit in einem Kessel gesammelt. Hier liegen keine besonderen Reinheitsanforderungen vor; allerdings ist wegen der Möglichkeit der Freisetzung gefährlicher explosionsfähiger Atmosphäre die Verwendung explosionsgeschützter Betriebsmittel, wie Langfeldleuchten (Zone 2), Sicherheitsschalter und Bedienterminals (Zone 1) vorgesehen.
Fazit
Mit der Reinraumtechnik und dem Explosionsschutz treffen sich zwei typische Nischenbranchen, die ihre Bedeutung aus der Besonderheit bestimmter industrieller Prozesse erhalten. Während die Reinraumtechnik den Produktschutz und den Personenschutz umfasst, ist der Schutz von Personen und Anlagen vor den gefährlichen Auswirkungen unkontrolliert ablaufender Prozessreaktionen Aufgabe des Explosionsschutzes. Die technischen und organisatorischen Anforderungen an die Reinraumtechnik und den Explosionsschutz sind im Wesentlichen unterschiedlich.
Zur Vermeidung unnötig hoher Kosten bei der Errichtung von Anlagen, in denen beides verlangt wird, ist daher eine frühzeitig einsetzende enge Zusammenarbeit zwischen dem Planer und Betreiber der Anlage sowie dem Hersteller der explosionsgeschützten Betriebsmittel notwendig.
Neuen Kommentar schreiben