Sichere Beförderung von Schwefeldioxid
Nigerias Industrie ist wieder um eine Petrochemie-Anlage reicher. Für dieses Großprojekt wurde unter anderem ein Prozessgasverdichter zur Beförderung von verunreinigtem und aggressivem Schwefeldioxid benötigt. Diesen entwickelte einer der Weltmarktführer für Turboverdichter für kleine Fördermengen und Zone 0-Maschinen. Eine wichtige Anforderung war es, den Verdichter für die Ex-Zone 2 zu konzipieren. Somit lag eine enge Kooperation mit dem Experten im Explosionsschutz, R. STAHL, nahe. Bei der Planung und Umsetzung sahen sich die beiden Unternehmen mit vier Herausforderungen konfrontiert:
- Kundenwunsch, die Elektrokomponenten in Ex d zu liefern.
- Anforderung an eine kompakte Schaltschranklösung.
- Der Verschleiß, bedingt durch die Beförderung von Schwefeldioxid.
- Berücksichtigung klimatischer Umgebungsbedingungen.
Energieversorgung in Ex d
Die Anforderung, alle Elektrokomponenten in Ex d auszurichten, hätte eine sehr kostenintensive, schwere und großräumige Lösung bedeutet. Um dem Kunden eine maßgeschneiderte Lösung zu präsentieren, die ihm Kosten und Platz einspart, wurden die technischen Spezifikationen genau analysiert. Daraus ging hervor, dass eine Ex d-Ausrichtung für die Energieversorgung ausreicht. Die für den Kunden optimale Lösung war somit die Kombination der Zündschutzarten Ex d, Ex e und Ex i. So wurde die Einspeisung in einem Ex d-Gehäuse zentralisiert und an einen Ex e-Schaltschrank mit den restlichen Geräten angebunden.
Kompakte Schaltschranklösung
Die Herausforderung, den Großteil der Elektrokomponenten gebündelt und kompakt unterzubringen, konnte souverän gelöst werden. Die Anzeigetafel der Zündschutzart Ex i wurde in einen Ex e-Schaltschrank integriert. Dieser beinhaltet Bedienfelder, sowie die Anzeigen zur Überwachung und von Fehlermeldungen. Dem Kunden wird durch den klaren und kompakten Aufbau das Handling wesentlich erleichtert.
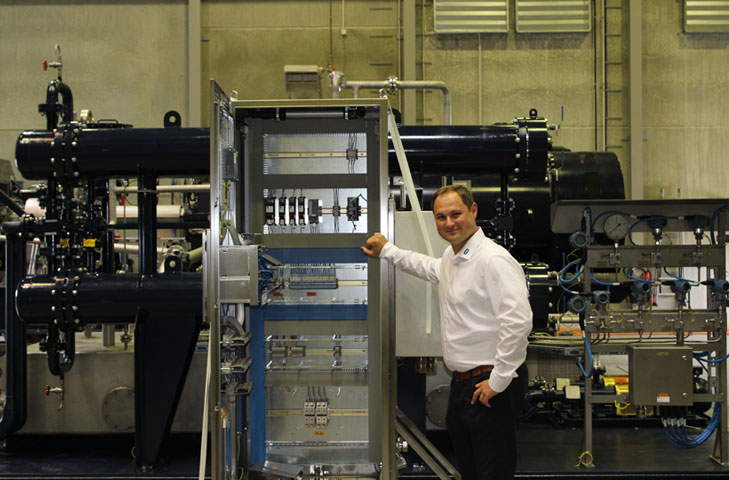
Reinigung während des Produktionsprozesses
Doch trotz optimaler Energieversorgung des Verdichters galt es, den allmählichen Verschleiß zu berücksichtigen. Denn bei der Beförderung des stark verunreinigten, aggressiven Schwefeldioxids lagern sich dessen Partikel im Laufe der Zeit unter anderem auf wichtigen Sensoren ab. Aus diesem Grund wurden die betroffenen Sensoren so in die Maschine integriert, dass deren Reinigung ohne Unterbrechung des Produktionsprozesses möglich ist. Die bis dato bestehende Standardmaschinenausführung mit Reinigungsöffnungen wurde modifiziert und auf den Durchfluss-Messungssensor ausgeweitet.
Des Weiteren lagern sich die Partikel auch am Laufrad ab, wodurch Unwucht entstehen kann. Diese verursacht wiederum Schwingungen, die sich auf die vorgelagerte Welle und von dort bis an das vorgeschaltete Getriebe übertragen können. Gelöst wurde dies mit einer zusätzlichen Lagereinheit zwischen Getriebe und Verdichter. Dies dient zum Schutz des vorgeschalteten Getriebes vor Schwingungen des Laufrads und verringert das Risiko eines irreparablen Getriebeschadens.
Edelstahl-Lösungen trotzen dem Klima
Die Qualität beider Weltmarktführer zeigte sich allerdings nicht nur bei der Entwicklung der optimalen und individuellen Kundenlösung, sondern auch bei der Auswahl der verbauten Materialien. Diese spielten beim Maschinendesign und bei den Elektrokomponenten, auch aufgrund der Umgebungsbedingungen vor Ort, eine wichtige Rolle. Küstennähe, gelegentliche Tropenstürme und allgemeine klimatische Bedingungen nehmen Einfluss auf das Material. Aus diesem Grund wurden für das Laufrad, dessen Gehäuse und die Schaltschränke widerstandsfähiges Edelstahl verwendet.
Fazit
Fachkompetenz, Flexibilität und Beratung zu jeder Zeit sind unter anderem Schlüsselfaktoren einer erfolgreichen Zusammenarbeit. Ob Standard oder maßgeschneidert: Wenn auch Sie vor einer Vielzahl von Herausforderungen stehen, dann finden wir gemeinsam Ihre Lösung.