Whether for a greenfield or brownfield site, good planning is essential for safe and well-functioning systems. Planning Ethernet-APL networks is new for many users. However, since Ethernet-APL has been developed for the process industry, it's easy to get started. In the end, "ease of use" was one of the most important user requirements when the new concept was developed.
The following 12 tips show how to approach the planning process and observe the basic rules of explosion protection.
1. Explosion protection? Zone classification comes first!
For systems in which there may be explosive atmospheres, special planning and documentation is imperative. To that end, the area with potentially explosive atmospheres is typically divided into zones (Europe ATEX or Global IEC, USA NEC 505) or divisions (USA NEC 500). There are cost-effectiveness reasons for this, in addition to the safety aspect. It means that you don't need to work with the highest possible – and therefore generally the most expensive – safety equipment everywhere in the system.
Division for explosive gas atmospheres into Zone 0, 1 or 2 (whereby the greatest risk is in Zone 0) occurs within the scope of ATEX and IECEx, and in the USA with NEC 505. In the USA, division generally occurs in accordance with NEC 500 into Class I (gases) and Division 1 and 2. Here, Division 1 is roughly equivalent to a combination of Zone 0 and 1.
Another important note: Zone planning is often dynamic, usually for modifications or changes to the system.
2. Where are Ethernet-APL devices installed?
Be it Ethernet-APL or a conventional field device, the field device must be placed at the point in the process where measurement or control takes place. Only selection of the type of protection may play a role. The great advantage here is that the intrinsic safety type of protection is used throughout Ethernet-APL installations. This is also suitable for Zone 0 installations, meaning the installation work, modifications, extensions, measurement, etc., are possible in operation under explosive atmospheres, without needing to disconnect the system or APL segment. Important: Every change must be documented.
3. And where do I install the Ethernet-APL field switches?
The field switches are required to set up an Ethernet-APL network and connect the field devices. A field switch is firstly a switch, as is required in any Ethernet installation. For Ethernet-APL, however, the field switch has a few additional tasks. The field switch supplies the connected field devices with intrinsically safe auxiliary power via a spur line, or "spur". These spurs have been limited in length to 200 m. Therefore, it may make sense to determine the network topology first and then position the field switches.
4. Which network topology shall I use?
That's a bit like asking, "Which came first, the chicken or the egg?". Should the field switches be determined first and then the network topology, or vice versa? Ethernet-APL essentially offers two options, star topology or trunk/spur topology. Both have their advantages and disadvantages that need to be weighed up. In short, it is a decision to either maximise the number of participants or to achieve the greatest possible distances cost-effectively. Currently, however, only field switches for the star topology are available on the market.
5. What is star topology?
Ethernet-APL can be installed in the star topology usual for Ethernet. This means that the field switches have been directly connected using four-wire Ethernet, such as 100BASE-TX, and the field devices are connected at their ports in a star shape in point-to-point connections. The field switches are supplied separately with auxiliary power. In a superordinate 100BASE-TX network, the distance between the field switch and automation system is limited to 100 m as is typical for Ethernet, which limits the whole network expansion. On the other hand, significantly greater distances of up to 20 km are possible with fibre optics, which optionally is supported by some field switches. Another advantage is that the higher-level network can also be set up in a ring topology, which increases the availability of the installation. Depending on the supplier, the field switches can be installed in the control room, in Zone 2 and also Zone 1.
6. What is special about trunk/spur topology?
Alternatively, trunk/spur technology can be used, which is familiar from field bus installations. The network transition from 100BASE-TX or –FX network occurs via a power switch here. This then supplies the Ethernet APL network including the field switches via a trunk line. The connected field switches in turn supply the field devices with intrinsically safe energy. The trunk line can be up to 1000 m, making it ideally suited for extensive systems. However, due to the voltage drop on the trunk line, precise project planning is required and the project planning must be checked and, if necessary, adapted in the event of changes. The more devices are to be operated on the trunk, the shorter the available cable length will be. The ring topology is not supported by the trunk. The field switches can be installed in up to Zone 1, the power switch typically in the control room or in Zone 2. The trunk is installed in the increased safety type of protection "e".
7. What more can I install in my Ethernet APL network?
A major advantage of the Ethernet-APL technology is that all Ethernet-capable devices in the same network work together without any problems. This means that non-APL-capable devices, i.e. classic 4...20 mA sensors and actuators, simple proximity sensors or solenoid valves, can also be integrated via remote I/O. Ethernet-capable remote I/O with PROFINET or EtherNet/IP, for example, has been available for several years and can be installed with the field switches in Zone 1. Similarly, wireless access points, which are increasingly required in Zone 1, especially for mobile solutions for maintenance and servicing. Local access to the network is a major advantage, especially with Ethernet, as there are otherwise few local troubleshooting options available.
Depending on regional requirements, overvoltage protection specially for large distances between the field switch and the control room may make sense, i.e. specially for a trunk connection over 1000 m. Whether the relatively short spur connections are also provided with overvoltage protection must be decided on a case by case basis. However, this would then be required on both sides on the field switch and on the field device port. In addition, plug connectors are permissible, for example for maintenance purposes in the mains. The maximum number of these inclusions are listed in Table 4-6 in the engineering guide.
8. And is the automation system simply connected "on top"?
In principle, yes – it is connected directly above the Ethernet backbone for the star topology. For the trunk/spur topology, it is connected via the power switch. It is important to know that for the trunk/spur topology, the network expansion must be designed accordingly, since the voltage drops in the system influence the expansion depending on the power of the power switch, current consumption of the field devices and the dimensions of the cables. The engineering guide provides support here too, for example in Chapter 4.10, with best-practice examples. With the star topology, the number of possible participants per network is actually only limited by the performance of the automation systems used.
9. Does Ethernet-APL have the problem of network overload?
Yes and no. In process technology systems, the network load should ideally be below 10% for the process control system. With star topology, this is below 5% for process-typical cycle times of 400–500 ms for 250 cycle field devices – that's enough reserve! For trunk/spur topologies which are suitable for approximately 50 field devices thanks to the aforementioned voltage drops on the trunk, this is as low as 1% under the same conditions. To err on the side of caution, research is underway as regards what could happen under extreme conditions and how this can be dealt with.
In practical tests, installations with over 200 APL field devices have already been operated via PROFINET on one controller without any problems. The practical tests as well as various theoretical studies show that Ethernet APL is a very robust physical layer and can easily cope with extreme requirements. This makes it ideal for process automation.
10. How does verification of intrinsic safety work again?
Verification of intrinsic safety is also required in Ethernet-APL networks, but this is very straightforward. With Ethernet-APL, exactly one energy source is connected with exactly one energy sink via a defined cable. With these framework conditions, the Ex i verification can be carried out exemplarily, i.e. once, on the basis of IEC 60079-25 "Intrinsically safe systems" for all interconnectable devices. So that not every user or planner has to do this again themselves, the Ethernet-APL working group together with the DEKRA exam has already provided this proof and documented it in IEC TS 60079-47: "Equipment protection by 2-wire intrinsically safe Ethernet concept (2-WISE = 2-Wire Intrinsically Safe Ethernet)". This TS (Technical Specification) will be integrated into IEC 60079-11 Ed. 8 and IEC 60079-25 Ed. 3 in the coming years, but can already be used today for the development and practical use of Ethernet-APL devices.
11. Why is verification of intrinsic safety becoming easier?
For users and planners, the following applies: If the devices used have been certified in accordance with 2-WISE, which is labelled in the EC Type Examination Certificate as well as on the device itself, the interconnection is intrinsically safe. Of course, as before, checks must be carried out to ascertain whether the devices are also suitable for the explosive atmospheres determined at the beginning, whether the ports have the correct type of protection (i.e. ia, ib or ic) and whether the installation location is correct. However, no calculations or cable dimensions have to be carried out.
It is also important that this very simple proof is documented accordingly in the explosion protection document.
12. What's last?
Something that is often forgotten, or at least that people don't like doing – documentation. All planning, investigations and verifications – including later modifications and extensions – must be documented. This is especially the case for systems with explosive atmospheres. Therefore, information such as zone classification, selection of devices and the simplified intrinsic safety verification with 2-WISE must be recorded in the explosion protection document, also including network information, such as IP addresses, etc.
This paves the way for safe operation of an Ethernet-APL system.
Further Reading:
These articles might also interest you
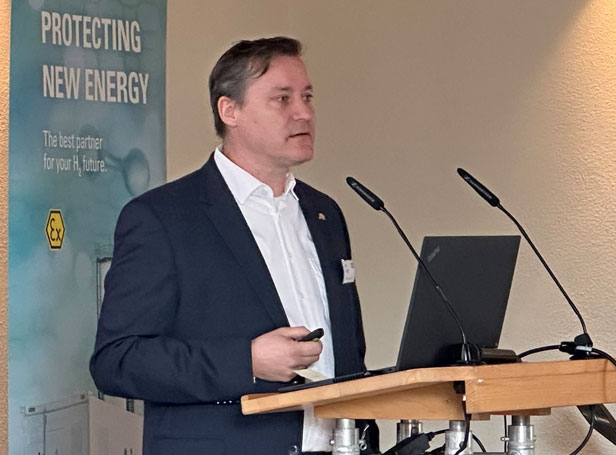
Write new comment