1. Is SPE (Single Pair Ethernet) and Ethernet-APL (Ethernet Advanced Physical Layer) the same?
That is definitely not the case, however, they are somehow related to each other. IEEE standardizes communication of various Single-pair Ethernet at different speeds and cable lengths. These meet the requirements of a variety of applications such as in-vehicle communication, discrete manufacturing, building automation, and process automation. In addition to communication, the entire physical layer from cable to connectors and from power supply to installation rules must fit for purpose.
Ethernet-APL deploys one standard from SPE, i.e. 10BASE-T1L and adds definitions for the physical layer to meet the requirements of process automation. The vast attention that Ethernet-APL has received is because its standardization is exhaustive and complete from connectors to cables to intrinsically safe power and explosion protection to conformance testing. In addition to this, a comprehensive engineering guide provides best practices, and Ethernet-APL is ready for deployment by all users of and vendors to the process industries.
2. Why does Ethernet-APL require a conformance test?
Ethernet-APL defines various types of ports such as Trunk/Spur, Source/Load, and so on. Each port type has its own specification and parameters that must be adhered to. The conformance test ensures interoperability of valid combinations of port types across all vendors by testing the behavior of the port across different types of instruments and infrastructure components based on the Ethernet-APL port profile specification. This ensures plug-and-play interoperability. It is important to note that since Ethernet-APL specifies the physical layer only, that the complete validation includes conformance testing for the communication protocols as well.
Four standards development organizations (SDOs), inclusive of FieldCommGroup, ODVA, OPC Foundation, and PROFINET/PROFIBUS International, are involved in Ethernet-APL. The SDOs provide Ethernet-APL conformance testing as part of their protocol certification process. Members of the SDOs have free access to the Ethernet-APL specifications.
3. Why separate specifications for Trunk and Spur?
The spur definition specifies a lower signal strength for the intrinsically safe (Ex i) interconnection compared to the trunk that is designed for increased safety (Ex e) installation and should bridge must longer distances. The reduced intrinsically safe signal power allows for more intrinsically safe supply power available to the instruments while still enabling a cable length of up to 200 meters between field switch and instrument. The two signal specifications provide a simple engineered system that ensures interoperability. Field switches installed in a field junction box provide connectivity in a convenient place, which is common and well known to work crews.
4. What is this Field Switch used for?
The field switch is a core component in an Ethernet-APL network. For Ethernet installations and connection of devices, switches are required. The Ethernet-APL Field switch does this but some additional things, too. Since Ethernet-APL provides explosion protection with intrinsic safety, some kind of intrinsically safe barrier or isolator is required. This is the second role of the field switch. A field switch is connected either to a 4-wire Ethernet network, the so-called star topology, or to a powered trunk line with increased safety type of protection, the trunk-spur topology. In both cases, the field switch operates as the I.S. isolator and converts the non-I.S. signals from the top down to the intrinsically safe spur lines. But there is more, the field switch also operates as the diagnostics center in an Ethernet-APL network with direct connection to the DCS and Plant Asset Management level. As the field switch is somehow situated in the center of such an installation with connection to the field devices and connection to the upper network, all the network information runs via the field switch, both physical and logical. This makes the field switch the ideal tool for network diagnostics, readable via WebServer, FDI packages or OPC UA – depending in the individual implementation.
5. What redundancy concepts does Ethernet-APL support?
The field switch provides point-to-point connections to the instruments with max. 200 m distance. Field switches with 4-wire Ethernet connection on the top level network support redundancy of the infrastructure with the media redundancy protocol, (MRP) or device level ring (DLR). With PROFINET communication, the MRP ring can be used also for S2-redundancy. The switches are easily configured for such redundant logical connections since the data just passes through the infrastructure, e.g. an instrument can maintain multiple communications paths to controllers to enable controller redundancy. It is also possible to implement redundancy in your application. Examples include installing homogeneous redundancy (two transmitters of same type) or diverse redundancy (two transmitters of different types to avoid systematic failures in a device). The redundancy on the powered trunk with dual lines or a ring is not yet available with Ethernet-APL.
6. In which explosive atmospheres can Ethernet-APL be installed?
Ethernet-APL definitions enable application and installation in any hazardous area. The possible installation of field devices and field switches depends on the manufacturer’s design of the product and is not related to Ethernet-APL technology. The new intrinsic safety concept for the Ethernet-APL spurs, called 2-WISE (2-Wire Intrinsically Safe Ethernet, IEC TS 60079-47) and the port profiles allow for intrinsically safe circuits corresponding to “ia” type of protection – which is suitable even for Zone 0, Zone 20 or DIV 1 installations.
7. Is Ethernet-APL the designated solution for explosive atmospheres and SPE for everything else?
While both technologies could be used either for the one or the other or for both applications, Ethernet-APL is optimised to meet the needs of process plants and specifically for hazardous areas with various options for explosion protection, including intrinsic safety. It is not impossible to use it in standard industrial applications as well – but therefore at a higher cost and with some restrictions on connectors and cables. SPE could be used in explosive atmospheres as well but not with intrinsically safe field devices. Other types of protection like flameproof “d” or pressurised “p” enclosures work with SPE but offer less flexibility for installation and maintenance. The choice of technology should be based on practical and economical requirements.
8. Is it possible to connect non-explosion protected/non-intrinsically safe field devices in a Zone 0 or 1 environment to an Ethernet-APL field switch with intrinsically safe spurs?
The Ethernet-APL field switch can be understood as the intrinsically safe barrier or isolator for intrinsically safe Ethernet-APL field devices. The energy at the field switch ports is limited to values conforming to intrinsic safety (see ignition curves from IEC 60079-11). However, the device that can be connected to such a port also needs to comply to the intrinsic safety standard to make sure that device internal temperatures and energy storage are well below the acceptable intrinsic safety values. This means that Ethernet-APL field devices need to get their intrinsic safety parameters and behavior certified for the respective place of installation.
9. Does the 2-WISE standard IEC TS 60079-47 substitutes the “classic” I.S. standard IEC 60079-11?
No, it does not; it is a kind of extension of it. To simplify engineering work and the required verification of intrinsically safe loops, a new technical specification (TS) standard was developed, the IEC TS 60079-47 “2-WISE, 2-Wire Intrinsically Safe Ethernet”. This extends the IEC 60079-11 and is based on IEC 60079-25 “Intrinsically safe systems” and the FISCO (Fieldbus Intrinsically Safe Concept, part of IEC60079-11 and -25). A field switch port that is (additionally) certified according to 2-WISE can be connected to 2-WISE field devices without calculation of intrinsic safety / entity parameters. In addition, the field switch may be certified to other types of protection as well, depending on the place of installation and required explosion protection.
10. Is 100BASE-TX-IS the same as Ethernet-APL or a competitive solution?
Actually neither of these. While Ethernet-APL is based on a 2-wire cable with intrinsically safe supply for field devices, 1000 m cable run, and 10 Mbit/second bandwidth, 100BASE-TX-IS focuses on other applications. It is based on a standard 4-wire Ethernet network with 100 Mbit/second bandwidth with only 100 m distance and without integrated supply for devices. 100BASE-TX-IS is based on the IEEE 100BASE-TX specification and just adds an intrinsically safe front end to it, enabling 100BASE-TX devices (with external power supply) to be connected to such intrinsically safe networks. Even a combination of 100BASE-TX-IS as a fast backbone with Ethernet-APL as the field device interface may make sense.
11. Why are the Ethernet-APL field switch ports limited to 0.54 and 1.11 W but the 2-WISE concept allows for 5.32 W?
The IEC TS 60079-47 allows an intrinsically safe load of up to 5.32 W for power input Pi of field devices. This value is identical to the FISCO value and allows the use of Ethernet-APL and FISCO field devices, like e.g. PROFIBUS PA devices, on a field switch from an intrinsic safety design point of view. The defined Power Classes 0.54 W or 1.11 W are based on minimum nominal values. It was decided to limit the available energy per port to make product design, intrinsic safety certification, and engineering easy with a limited set of well-standardized field device parameters and with this, limit the number of possible variants. As well as to not require any cable calculations (due to voltage drops etc.) while allowing as many field devices as possible in one network. Any field device that complies to the described power classes will be interoperable to appropriate field switch ports without the need to do any calculations.
12. Can I re-use my existing cables?
Likely! The cable must be shielded for reliable communication. The reference cable is the category IV cable that relates to the type ‘A’ defined by IEC 61158-2 (MAU types 1 und 3) which is widely used in process industries, e.g. in fieldbus installations. Many users can re-use this installed cable base. Because of the higher frequency range, which is not explicitly specified for most cable installed today, the experts highly recommend testing the installed cable. This is even more important if shielded cable other than type ‘A’ is considered for re-use. A reduction in usable cable length should be expected, as with the lowest acceptable quality for Ethernet-APL cables category I, the trunk is reduced to 250 m and the spurs to 50 m. For more conformance information, refer to the Ethernet-APL engineering guideline.
13. How do I implement network safety and security?
Safety and security must be considered from the system perspective. Like any other physical layer, Ethernet-APL transports application-layer safety and security services from the leading industrial automation standards bodies, which utilize standards such as IEC 61508 and ISA/IEC 62443. Network architects which design the infrastructure for the entire plant can deploy the same techniques and working procedures for the field of process plants. Of course, the communication protocols used in an Ethernet-APL network must support adequate safety and security measures. Means in a PROFINET or Ethernet/IP based communication network, the PROFIsafe profile or the CIP safety protocol has to be supported by the field devices and the connected logic solvers. The field switches in between do not have any influence on the safety or security quality.
Further Reading:
These articles might also interest you
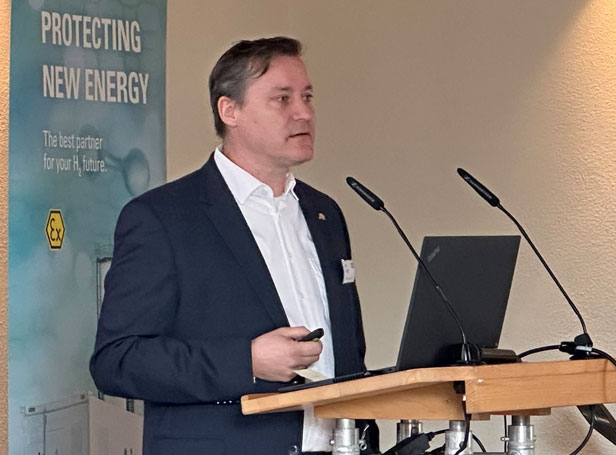
Write new comment