With the new digital twin platform for digital nameplates, R. STAHL is providing a perfect example of how asset administration shells can be used to create benefits when planning and operating devices in the process industry. In this interview, Roland Dunker explains which users stand to gain the most from this.
1. Mr Dunker, what were the main considerations and reasons for developing your new platform?
We were motivated by the idea of creating a platform designed exclusively for users of asset administration shells. We wanted to offer a solution which works regardless of download areas or standard platforms. Our platform is designed to address the specific needs of different users – regardless of their level of experience.
2. How have you taken the needs of the different user groups into consideration?
We put a great deal of thought into where data is created – completely separate from the system in which and the methods with which it is recorded, saved or shared, and what the access rights are like. We simply looked at where data is created, how it is used and what you can do with it. From these use cases, we then considered what should be linked with a digital twin to offer maximum benefits for users. This resulted in six use cases – and discussions over the past two years have shown that we have struck a chord with industry.
3. What sort of feedback did you receive at ACHEMA?
Customers confirmed that the requirements we are addressing are relevant. They expressed a clear need for complete information which doesn't have to be copied from a PDF file first. The data chains have to be complete. The data on engineering platforms usually isn't up to date either because it has not been possible to represent the life cycle until now. In the field, you need direct access to the right documents and information, not to PDFs with 300 pages. You have to know what successor products are available, as this affects the downtime. The industry needs this information and, by linking the data, this is precisely where we are creating added value. The issue of firmware updates for smart products is also important. Companies confirm that they have to check for security vulnerabilities but don't have the resources to do this. Operators are also faced with ever-increasing regulations – more and more has to be documented and versioned documents should be available at all times. At the same time, they have fewer employees. This is why our customers are grateful for any digital solution that can make their lives simpler.
4. Your platform only covers devices from R. STAHL, but companies are likely to use many devices from other manufacturers as well. Does it still make sense for them to use your platform?
Of course. Even if just one product has an asset administration shell, this still offers huge benefits for service engineers. Maintenance information often comes from PDF documents – but the data also has its own history. We publish the maintenance data and transfer it to the PDF file if there is no asset administration shell. The system manufacturer has to copy all maintenance information, add their own instructions and then pass all this on to the operator, who has to transfer everything into their service software manually. This involves a lot of work. With our IEC 61406-compliant solution, the engineer simply has to scan the rating plate and therefore identify the asset in the service software. They have a clean database, don't have to assign separate tags, and can access the information they need directly.
We show how easy integration is, and that's what sets us apart. When comparable products are available, the time and effort required for integration is an important deciding factor. If a device manufacturer only offers a data sheet, then a lot of integration work is required. Many process operators realise that the asset administration shell is establishing a cross-industry standard aimed at resolving precisely these issues.
5. So is this a unique feature which will lead to people choosing R. STAHL products over those from competitors?
Definitely! Customers are impressed by the ability to simply scan the rating plate in the field and have direct access to all data and documents, know the maintenance status on-site and see successor products if service is required. By offering this option, we are positioning ourselves as a technology leader. And we are even meeting some of the requirements of the future Ecodesign for Sustainable Products Regulation (ESPR).
6. What challenges do you see in the implementation of the EU regulations relating to the digital product passport?
In many companies, the greatest challenge relates to the quality of the master data. This data has built up over time and often hasn't been managed or updated well. However, a standardised and high-quality database is the foundation of successful digitalisation. Once this is in place, transforming it into an asset administration shell or other formats is a relatively small step. Businesses have to do their homework now and invest in data quality.
7. What specific steps do manufacturers and operators have to take now to prepare them-selves for future challenges?
Manufacturers and importers must ensure that their products have a digital product passport by 2026. As a result, operators will also recognise the benefits of digitalisation and retrofit their existing systems. In both cases, the first step that needs to be taken is comprehensive data cleansing and standardisation to put the conditions in place for the asset administration shells.
8. Can you quantify the economic benefits in the engineering process?
Let's take an example from the pharmaceutical industry: We know from a company which develops bioreactors that fully digital engineering makes the development processes far quicker. The planning process is normally sequential, but working with simulation and 3D models in parallel has made it possible to save several years of development time. This is invaluable.
Technicians and engineers save on average around one hour per asset when entering device data into engineering tools.
9. Are plans already in place for the future development of the platform?
We have a complete roadmap with various use cases. For a start, we will expand search models which cover product and engineering aspects. We have three levels of complexity for our products: Components, configurable products and custom engineering. We create tailored solutions for customers and integrate data from suppliers. In the long term, we will meet all of the requirements associated with the digital product passport and make all of the necessary data available.
Further Reading:
These articles might also interest you
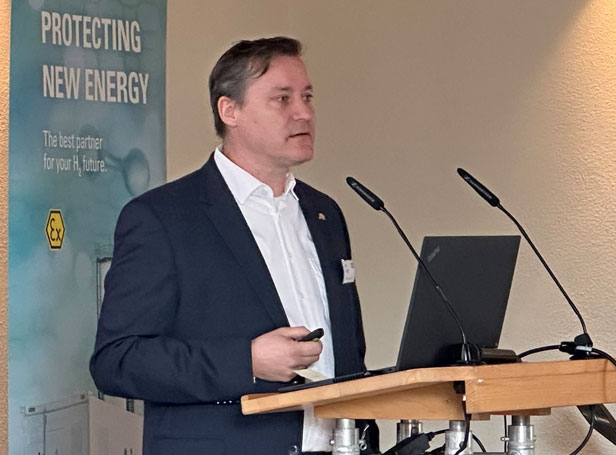
Write new comment