When it comes to consistent communication, Ethernet is the perfect choice. But typical Ethernet technology cannot meet the requirements of the process industry. As a result, an open standard has been developed on the basis of a new physical Ethernet layer in order to make Ethernet suitable for use in the harsh everyday environments of the process industry: Ethernet-APL. André Fritsch is playing a key role in this development and in this interview, he gives us a glimpse behind the scenes.
Mr Fritsch, what was the driving force behind the development of Ethernet-APL?
André Fritsch: Ethernet-APL is the implementation of 2-wire Ethernet for the demands of process automation. The demand for 2-wire Ethernet originated in a few places, including the automotive industry. This demand required 2-wire Ethernet, which already meets 80% of the demands of the process industry. The technology was developed further, based on this starting point, and expanded to fulfil the specific requirements of process automation. These include, in particular, the implementation of explosion protection up to Zone 0, adapted installation technology to withstand the harsh environmental conditions, sufficient power to supply around 50 field devices with energy, and the ability to bridge great distances of up to 1000 metres.
What advantages does Ethernet-APL offer?
André Fritsch: The new technology has been designed for use in hazardous areas. Field devices can be operated using the intrinsic safety type of protection, which is preferred in the process industry. Another benefit is the fact that it is based on IEEE Ethernet. This is an international standard, which is continuously developed further by corresponding authorities and user groups. It also enables simple integration, both inside the system and between devices.
In addition, operators can use Ethernet-APL to bridge distances of 1 kilometre with a comparably high data transfer rate – a quantum leap compared to previous technology. This expands the potential application range to include additional and improved diagnostics.
Can you be more specific?
André Fritsch: Using typical 4 to 20 mA installation, operators can receive a maximum of two diagnostic messages – either everything is working or something is wrong. Using Ethernet-APL, they can learn precisely what has gone wrong and why, including troubleshooting recommendations. Alongside the improved evaluation options, significantly more remote diagnostics tasks can be performed. This means that systems can be operated significantly more cost-effectively.
Furthermore, the data is always available right where it is needed – such as on a tablet in the field, connected to the field device network. Seamless data exchange improves the consistency of this data. Ethernet-APL enables consistent data exchange between project engineering, control and asset management systems.
What's more, quick and easy access to data offers a closer look at processes, thereby providing an opportunity to optimise these processes, for instance using smarter data analysis. In addition, new maintenance concepts are available because the field devices are able to automatically report required maintenance more easily and quickly, among other benefits.
Ethernet-APL makes processes more cost-effective, simpler and safer, and avoids inconsistencies in data.
Process automation specialists tend to be quite risk-averse. How do you hope to convince them to use Ethernet-APL despite this?
André Fritsch: Previous installations in the process industry can continue to be used without any problems. However, operators can also use a second channel to improve monitoring and diagnostics in order to gain corresponding experience and see the benefits of this new technology for themselves. The advantages and opportunities offered by this new technology are sure to convince even the most reluctant of operators.
The Ethernet-APL project has existed since 2011. Why has it gained so much traction in the last few months?
André Fritsch: Ethernet has been used in the process industry for some time now and solutions for hazardous areas have also existed for a number of years, primarily in new systems. However, no digital systems can be built using an Ethernet infrastructure alone. This requires suitable field devices and suitable communication protocols. The Ethernet-APL project has succeeded for the first time in bringing manufacturers and standardisation organisations together. This has sent a clear signal to others, which means that users are seriously considering how they can use this technology. Of course, this results in a certain amount of pressure on the Ethernet-APL project team to complete the specifications and then make corresponding products ready for the market for manufacturers. This is why we might get the impression that the project is only just starting to gain steam. In fact, the team has been working intently on the project from the very beginning. Otherwise, we would never have made this much progress.
Are there any technological sticking points for Ethernet-APL?
André Fritsch: The main difficulty has been the cabling. This has been defined within the context of Ethernet-APL. To cover distances of 1000 metres using a 10 MBit/s network, correspondingly high-quality cables must be used. One aim of the specification was to ensure that the type A cables used in fieldbuses can still be used, as it can be difficult to replace these in existing systems. This is linked to the correct planning and installation of Ethernet-APL segments. Even though this is no more complicated than typical fieldbus installation, for instance, the project team were convinced that offering corresponding support for planners, integrators and installers was an important goal from the very start. To do so, we created a comprehensive engineering guide at the same time as the technical specifications, which covers planning- and cabling-related aspects, as well as explosion protection.
What role does R. STAHL play in the Ethernet-APL project?
The topic of explosion protection is, of course, very important for us. This means that we bring our expertise to the table when developing the technical specifications, ensuring that user benefits and practicality are the top priorities during development. At the IEC level, we actively worked on the new Ex i specification – IEC TS 60069-47 "Equipment protection by 2-wire intrinsically safe Ethernet concept (2-WISE)". We also made significant contributions to the explosion protection-related content in the engineering guide mentioned earlier. Furthermore, it is our job to develop the products that are required for installation technology in the field, such as the Ethernet-APL field switches and power switches suitable for Zone 1.
The first Ethernet-APL prototypes have already been developed. What do the next steps look like?
André Fritsch: Corresponding tests will be performed using the prototypes from field device manufacturers and alongside operators. The lessons we learn from these tests will be fed back into the development process in order to further optimise the products. At the same time, we are currently performing extensive performance and interoperability tests – these will ensure that, at the end of the process, we have a compatible technology of outstanding quality. These devices will then also be used for the planned conformance tests by the FieldComm Group. So far, all our results and feedback have been extremely positive. As a result, I estimate that the first products will be available in 2022 and corresponding systems will be fitted with Ethernet-APL from 2023 onwards.
Further Reading:
These articles might also interest you
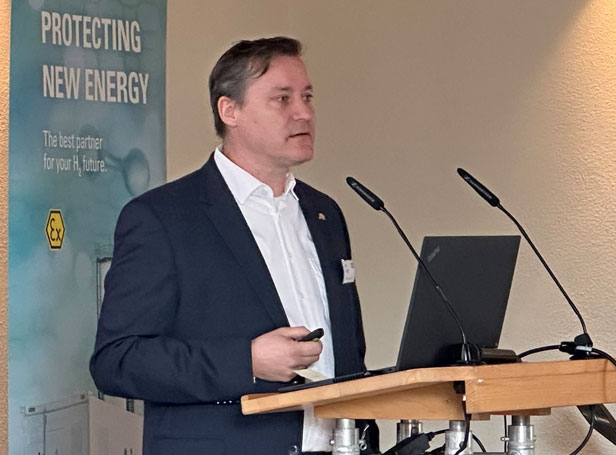
Write new comment