How can you, as a plant operator, protect your system from explosions? For the answer, look no further than the explosion triangle, which is made up of a combustible material, oxygen and a source of ignition. According to this triangle, at least one of these three factors must be eliminated or reduced.
Ten primary explosion protection methods
Avoiding a hazard entirely is better than any form of protection. For this reason, your first port of call should be to implement primary explosion protection methods. These aim to prevent the formation of an ignitable atmosphere. There are a number of potential methods to achieve this:
1. Avoiding the use of combustible materials
Whenever possible, you should use materials that cannot form an explosive mixture instead of combustible substances. For instance, solvent-based paints can be replaced with water-soluble paints.
2. Reducing the use of combustible materials
Another option is to limit the use of combustible materials to a safe extent, so that no explosive atmosphere can form.
3. Using materials with as high a flash point as possible
The flash point is the lowest temperature of a combustible liquid at which a flammable vapour-air mixture forms over the liquid level. If the flash point is far higher than the maximum temperature that will arise, no explosive atmosphere can form.
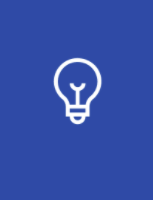
Flash point petrol
4. Reducing the processing temperature
This method ensures that the processing temperature is kept significantly lower than the flash point, for instance using cooling.
5. Limiting the concentration of combustible materials
In order for an explosive atmosphere to form, the combustible substance must be present in a certain concentration range. If the concentration is too low (thin mixture) or too high (rich mixture), no explosion can occur. The mixture can only react to ignition and cause an explosion in the range between the upper explosion limit and lower explosion limit.
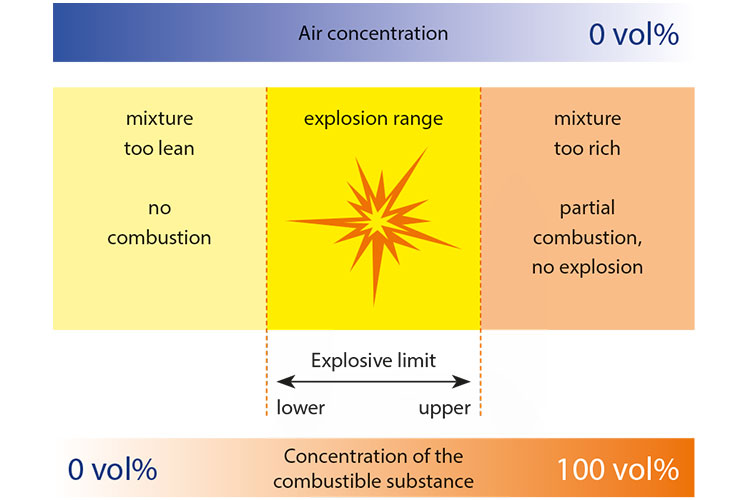
In the case of explosive dusts, the key is to stay below the lower explosion limit, which is between 15 and 100 grams per cubic metre.
6. Inertisation
Limiting the concentration of the oxygen content reduces the reactivity of a combustible material. This can be done by adding inert gases such as nitrogen. The aim of this process is to reduce the oxygen concentration in the mixture until it is no longer explosive.
7. Closed systems
Closed systems of this kind are used at petrol stations, for example. Here, the gas displacement procedure is used with two separate hoses – one for petrol and one for extracting gases.
8. Technically leak-tight systems
Systems that are technically leak-tight ensure that the explosive substances cannot escape from the system. This prevents the formation of an explosive atmosphere outside the equipment.
9. Ventilation
Natural or technical ventilation can also prevent or, at least, reduce the formation of hazardous explosive atmospheres.
10. Concentration monitoring
Monitoring the gas concentration, for example using gas warning devices.
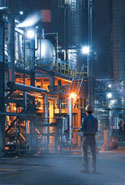
Write new comment