Every technician and every engineer is familiar with the situation, and nobody likes it: In industry, returns are par for the course – for instance, sensors may need to be calibrated by an external laboratory or products may need to be inspected, repaired or modified. In practice, there are many different reasons why a product might need to be returned.
One constant, on the other hand, is the fact that each manufacturer has their own return forms and requires that these be used as part of the proper returns procedure. However clear the manufacturer's requirements are, the returns process is nevertheless a laborious one for the customer. First, the customer must find the correct form on the manufacturer's website. If they manage to locate the appropriate form, they must then manually enter a great deal of information. Besides the product designation, the order number and the serial number, additional attributes are often required in order to identify the product. The sender's details, reasons for the return, and in many cases, a clearance certificate are also required. Once the customer has entered all this information into the form, it often needs to be e-mailed or submitted online and enclosed with the product. All in all, doing things manually like this involves an excessive amount of work, which often takes far too long.
Documents that have been filled in by hand are also a huge headache for the recipients. It is often quite a challenge to decipher people's handwriting, check the data and transfer it to the maintenance software. The forms frequently contain errors, for example the order number and serial number are sometimes mixed up, the wrong recipient address is sometimes selected (where there are multiple production sites), and letters and numbers are sometimes transposed.
The B2C sphere benefits from significantly better returns procedures. Unfortunately, there is only limited scope for reproducing these exactly in a B2B environment. The use of digital nameplates in conjunction with asset administration shells offers a vast improvement. If a customer needs to return a product, all they need to do is scan the QR code on the product. This opens the manufacturer's customer platform, which contains all the available data for the product (asset) that corresponds to that specific serial number. The "Create return shipping note" function can be used to have all the required data that is known about the product automatically retrieved and presented in a pre-populated return form. All that remains now is for the technician or engineer on site to enter the sender's contact details, state the reason for the return and complete the clearance certificate. They can then send the form directly to the manufacturer and print it out.
This is how to make smart, simple, time-saving returns processes a reality in industry – there is no need to search for the appropriate forms or enter information that is already held, so a return can be arranged within a matter of minutes.
Further Reading:
These articles might also interest you
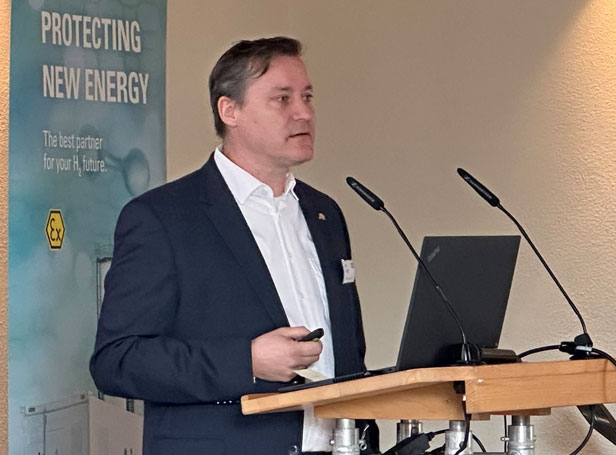
Write new comment