We're all familiar with static electricity. It's what makes a piece of clothing crackle when you put it on. The phenomenon of electrostatic charge and the effects of discharge are all around us in everyday life. In this context, the effects are usually limited to that familiar crackling noise, hair standing on end, or a slight shock just before touching a door handle. It's not pleasant, but it's not hazardous. Thunderstorm lightnings, by contrast, are a formidable and dangerous force of nature, and are also caused by electrostatic charge.
Electrostatic discharge in hazardous areas
The build-up of electrostatic effects in hazardous areas can become a major hazard, even when only low amounts of energy are involved. The energy released by a discharge is, in many cases, enough to ignite an explosive atmosphere. For this reason, electrostatic discharge is a potential source of ignition and must be considered and assessed by the system operator in accordance with the German Ordinance on Hazardous Substances (GefStoffV). The importance of this issue is reinforced by the long list of accidents that can be caused by electrostatic discharge.
What is electrostatic and how is it generated?
Static electricity refers to a stored or latent electrical charge. The electrostatic charge is usually generated by a process known as charge separation, when two previously joined materials are separated. The friction of this process represents just one special form of contact, during which the number of contact points increases and the distance decreases. The condition that must be met in order for discharge to occur is that two materials with different electron discharge energy come into contact with one another (for instance, metal and insulating plastic). When this occurs, some of the electrons pass from one material to the other. The subsequent separation results in one negatively charged material with excess electrons and one positively charged material with too few electrons. The discharge can be measured as electrical voltage.
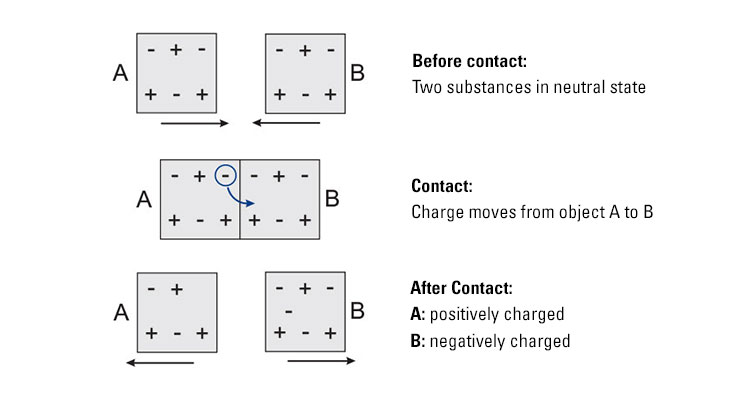
The strength of this voltage depends on a number of factors. As well as the speed of the separation or friction, the size of the surface and the conductivity of the materials involved are also crucial. To generate a charge, at least one of the two materials must be slightly conductive. The charge itself can also be transferred to a conductive object and stored there.
Liquids are not immune to this effect. A fluid flowing along a solid material can generate a charge. To do so, the liquids must contain ions as charge carriers. The amount of charge is also determined by the specific conductivity and flow speed for liquids.
Another effect that can lead to a charge building up is the induction charging. This effect is created by an external electrostatic field acting on an object. The strength of this field leads to a charge displacement in the body that is exposed to the field.
What processes can generate an electrostatic charge in a production facility?
Charges can build up at a number of points in the production facility of process technology systems, for instance as the result of staff moving around in non-dissipative clothing and shoes. Even these charges can damage electronic components and even lead to ignition, as a number of accidents at filling stations demonstrate.
Processes involving significant charge are even more dangerous. These include using a conveyor belt, and mixing or filling liquids and bulk goods. Particular caution is required if any of these substances are combustible materials, since this could lead to an explosive atmosphere and a potential source of ignition coming into contact.
One discharge is not necessarily like another
A discharge is a sudden charge equalisation. Depending on the configuration, different types of discharge can occur. These differ in the amount of energy released and therefore the danger of an ignition:
Brush discharge:
Brush discharges involve low energy. They can occur if a charged object made of insulating material is brought near an object made of conductive material. The amount of energy released is heavily dependent on the size of the insulating surface. By limiting the surfaces, the amount of energy can be reduced so that it cannot ignite an explosive atmosphere. For this reason, surfaces made of insulating material are limited.
Spark discharge:
A sudden discharge from a charged object made of a conductive material to another object made of a conductive material is referred to as a spark discharge. A spark discharge can always become a source of ignition.
Corona discharge:
This form of discharge occurs between sharp edges or corners of conductive materials if a field strength of at least 3 MV/m is present. Since the amount of energy is significantly lower than that of a spark discharge, the resulting risk of it acting as a source of ignition is relatively low.
Propagating brush discharge:
Propagating brush discharges involve the most energy. The high charge density required for one to occur results from extremely thin insulating objects, such as films or coatings. The low distance between the upper and lower side leads to attraction between the positive and negative charges, enabling a high amount of energy to be stored. The energy of these discharges is capable of igniting all explosive atmospheres based on combustible liquids and gases, as well as combustible dust mixtures. These discharges can be prevented by using materials with a breakdown voltage of less than 4 kV.
Bulking brush discharge:
This form of discharge can occur in the upper part of a cone of bulk goods, such as the cone that is created when filling a silo. It requires an insulating, highly charged bulk good.
The silos or large containers are typically made of a conductive material. Factors such as the grain size, conductivity, bulk density, specific charge of the bulk goods and the filling speed all play a crucial role.
Type of discharge | Hydrogen, acetylene, etc. MIE <= 0.025 mJ | Solvent vapours MIE > 0.025 mJ | Dusts MIE > 1 mJ |
Brush | + | + | - |
Sparks | + | + | + |
Corona | (+) | - | - |
Propagating brush discharge | + | + | + |
Cone | + | + | + |
Discharge types as effective sources of ignition
General measures for preventing electrostatic charge
The conductivity of the materials is key to determining the amount of energy that is released by a charge and can therefore potentially become a source of ignition. For this reason, objects with surfaces made of insulating material should not be used in hazardous areas; additionally, work clothing for use in hazardous areas must have a resistance less than 100 M Ohm.
However, if equipment made of insulating material is used, the size of the insulating surface must be limited. These limiting values are assessed for an item of equipment within the framework of the EC Type Examination Certificate by the notified body. However, exceptions are possible and are identified using a stipulated label on the equipment and in the operating instructions. The user must ensure that these specifications are followed. The most well-known of these is the safety note stating that cleaning must only be performed using a damp cloth. The system operator must observe the limit values when assessing equipment on their own (e.g. when assessing it as simple apparatus or in the case of subsequent painting).
To ensure that equipment and objects cannot become charged by conductive or dissipative materials beyond a safe level, grounding or connection to equipotential bonding is mandatory. IEC EN 60079-14 and IEC EN 60079-32-1 stipulate a resistance of less than 1 M Ohm for temporary connections to ground. NFPA 77 considers conductive objects to be grounded if the resistance to ground is less than 1 k Ohm.
How safe is passive grounding?
Electrostatic grounding or bonding can be established using simple cables with suitable connection elements, such as clamps. However, it is important to remember that these grounding kits are subjected to heavy mechanical loads, especially in the case of temporary grounding. Often, they will fall to the floor and make their way beneath shoes or the tyres of forklifts and trucks.
However, the smallest mechanical damage to the conducting connection in the cable or clamp can lead to this safety equipment having no effect. Regular conductivity checks reduce the risk of this kind of damage going unnoticed. However, these checks involve additional work and it remains uncertain whether a loose contact would definitely be detected.
The contact between the clamp and the object to be grounded poses an additional risk. How safe is it if the clamp penetrates the coating or corrosion on the surface of a drum? Safe operation of the system is dependent on a number of factors, not least this contact.
Advantages of monitored grounding
The use of a monitoring device offers several advantages compared to passive grounding using a simple grounding kit. These devices establish and permanently monitor the connection between the equipotential bonding rail and the object to be grounded. This ensures that any absent or ineffective ground connections are safely detected. The status of the grounding is shown by an indicator lamp; additionally, on many devices, an additional contact can be used to stop loading directly or via an automation system.
A number of versions can be used to ground trucks and FIBCs – these additionally feature an object detection function. Once the devices are connected, this function enables them to detect whether they are connected to a truck or an FIBC – or whether the grounding clamp has only made contact with metal objects on the loading equipment. This detection system makes these applications significantly safer.
What must be considered when loading combustible liquids?
Electrostatic charges build up as soon as the liquids start moving, whether that is through pumping or mixing, or when loading or unloading containers. The extent of the charge is determined by the conductivity of the liquids, the characteristics of the tank and the flow speed. TRGS 727 contains detailed information about what to consider when handling liquids.
When loading road tankers, it must be ensured that grounding is performed before any covers are opened and before pipelines are connected. This grounding must have a resistance less than 1 M Ohm. Without additional grounding measures, this value will not be achieved. The connection to ground or equipotential bonding for the loading equipment must be present during the entire work process. The use of grounding equipment with a lock (i.e. automatic switch-off) is considered practical. On an international scale, IEC EN 60079-32-1 additionally requires the conductive connection between the connection point on the truck and the grounding point on the system to be less than 10 Ohm.
In the case of rail tankers, it can be assumed that sufficient grounding is established via the rails, due to their design. Despite this, the limiting values must also be complied with. In case of any doubt, additional grounding must be established.
Smaller containers (volume ? 1 m3) such as drums or IBCs should preferably be made of conductive or dissipative materials, which are connected to a ground potential before filling or emptying. The RIBCs consist of an insulating plastic tank, embedded in a metal frame. These must not be used for combustible liquids in explosion group IIC and IIB with a minimum ignition energy < 0.2 mJ. It must be ensured that versions that are specially designed for handling combustible liquids are used in this case. For instance, these have a cover and an outlet fitting made of dissipative material. The grid and outlet fitting must have a connection to ground.
When using these containers, it must be ensured that the measures for preventing electrostatic discharge are also implemented when non-combustible liquids are filled or emptied in an explosive atmosphere.
Caution when loading bulk goods
The grain size is a crucial factor in determining the ignition capability of bulk goods. The greater the grain size, the lower the ignition capability. As soon as the minimum ignition energy exceeds the value of 1 J, no additional measures to prevent electrostatic discharge must be taken. For finely-grained bulk goods, the specific resistance, humidity and conveying speed all determine the extent of the charge. It must be ensured that all conductive and dissipative parts of the system, including the containers, are grounded.
The use of flexible bulk goods containers are a special case in this regard. These containers are known as FIBCs (Flexible Intermediate Bulk Containers) or Big Bags. These containers are available in four different versions (A, B, C and D). Type A features no measures to reduce electrostatic charges. Types B, C and D feature design measures to prevent hazardous charges.
Minimum ignition energy (MIE) of the bulk goods
| Filling and emptying equipment is located in | |||
Non-hazardous area | Hazardous area in | |||
Zone 21 or 22 | Zone 2
| Zone 1
| ||
Not capable of dust explosion or 1000 mJ < MIE | A, B, C, D | A, B, C, D | C, D | C1, D1 |
3 mJ < MIE < 1000 mJ | B, C, D | B, C, D | C, D | C1, D1 |
MIE5 < 3 mJ | C, D | C, D | C, D | C1, D1 |
Dust with combustible solvent content3 | C2, D2 | C2, D2 | C2, D2 | C2, D2 |
1 When filling the FIBC only in conjunction with additional measures, e.g. purging with air.
2 When filling and emptying the FIBC only in conjunction with additional measures, e.g. inertisation.
3 For the concentration of the solvent content, see also no. 6.2.
4 If the handled bulk goods determine the zone.
5 The restriction to only use a type C or type D FIBC for bulk goods with MIE < 3 mJ is based on the ignition capability of cone discharges. These can possess much higher energy in a type B FIBC than in a type C or type D FIBC. If a type B FIBC is used, the cone energy can reach a value of 3 mJ, even for bulk goods with a median value of just 0.055 mm. In a type C or type D FIBC, the median value of the bulk goods must be 0.27 mm or higher, so that the cone energy reaches 3 mJ. Typically, however, bulk goods that are this coarse have a MIE higher than 3 mJ.
Thanks to their structure, type B FIBCs prevent the build-up of propagating brush discharges because the breakdown voltage for the insulating material is less than 6 kV. Other forms of discharge, such as brush discharges or cone discharges, may still occur.
Type C FIBCs contain dissipative materials, which ensure that the leakage resistance is under a value of 107 Ohms. This type of FIBC must be grounded. The use of a grounding monitoring device with object detection is recommended for grounding these FIBCs. Devices with this function monitor the correct connection to the Big Bag and ensure that operating errors are eliminated.
The principle behind type D FIBCs is based on limiting the charge to a safe extent, based on corona discharge. Evidence must be provided that no dangerous charges are generated. Conductive objects and people in the immediate surroundings must be grounded.
The movement of gases does not generate an electrostatic charge. Pneumatically conveying bulk goods is an exception to this statement. In this case, the specifications for conveying bulk goods must be observed.
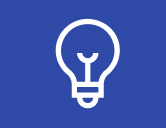
Write new comment