Ethernet-APL is in the process of becoming the digital backbone for the field level in processing systems. But what's the situation like with the functional safety infrastructure? In safety systems, does Ethernet-APL offer the same availability and reliability as 4 to 20 mA technology? And is Ethernet-APL not prone to cyber attacks? Time to take stock!
For decades now, established 4 to 20 mA technology has been relied on in the process industry and in safety-critical applications. This technology provides basic and reliable analogue signals for measuring and control circuits. However, it is reaching its limits ever more frequently, especially with regard to the requirements of modern Industrial Internet of Things concepts and the increasing networking of digital devices. Although the implementation of digital fieldbus technologies has improved the availability of diagnostics information, the integration of these systems is often complex. What's more, their data rate and data transparency are limited. Ethernet-APL is designed to do away with these drawbacks.
Why Ethernet-APL offers a better solution for functional safety
Ethernet-APL (Advanced Physical Layer) offers many advantages: It enables fully digital communication in the field level, is suitable for hazardous areas down to Zone 0 and boasts a transfer rate of 10 Mbps via a two-core cable. The technology makes it easier to connect field devices and means that the same cable can be used for the power supply and data transmission – with the "intrinsic safety i" type of protection for both. This considerably reduces the cabling required and the complexity compared to 4 to 20 mA technology. And that's not all – Ethernet-APL is fully interoperable with industrial standards like PROFINET and PROFIsafe, enabling seamless integration into existing systems.
Despite the obvious benefits of Ethernet-APL, users have some concerns, particularly with regard to reliability, cybersecurity and functional safety. The situation was similar when fieldbuses were first launched: The safety infrastructure was still set up with conventional 4 to 20 mA technology even in systems which used a fieldbus for process control. But because this makes implementation and maintenance more costly and complex, process operators have for some time now been looking for consistent digital communication where control technology devices and safety equipment use the same communication technology. And this is where Ethernet-APL comes in. But the questions asked at the outset still need to be answered.
1. Availability and reliability
Many users are asking whether Ethernet-APL offers the same reliability and availability as the established 4 to 20 mA technology. The answer is a clear "Yes". Ethernet-APL was designed specifically for industrial applications, including the harsh environments of the process industry. The technology supports topologies like star or ring structures which ensure high availability. If a device fails, the system remains stable because the ring structure makes alternative communication channels available. Field tests, such as those performed at BASF, have shown that Ethernet-APL ensures reliable communication even in SIL 3 applications. The PROFIsafe security protocol can be used with Ethernet-APL. PROFIsafe has a long track record of success in factory automation and can also be used in the process industry for the reliable transmission of safety-relevant data between controllers, sensors and actuators via Ethernet-APL.
2. Cybersecurity
Ethernet-APL is an IP-based technology, so security concerns about potential cyber attacks are legitimate. But if we compare Ethernet-APL with the previously used 4 to 20 mA technology using HART communication or fieldbuses like PROFIBUS DP or PA, it soon becomes apparent that these can be a relatively easy target for internal and sometimes also external cyber attacks. However, Ethernet-APL uses modern protocols with additional security functions, like PROFINET, which allow for secure communication by means of encryption and authentication. Using public key infrastructure (PKI) ensures that only authorised devices can access the network. What's more, denial-of-service attacks are warded off with defence in depth strategies which adopt multiple layers of security. Sophisticated protocol standards like PROFINET and OPC UA already offer mechanisms for safeguarding the integrity and authenticity of data.
3. Functional safety
Ethernet-APL is able to meet the same functional safety requirements as 4 to 20 mA technology. PROFIsafe, which is established as a successful safety protocol for industrial networks, enables the safe exchange of data between controllers and field devices. SIL 3-certified solutions are already available, as demonstrated by a test set-up at BASF in Ludwigshafen: This proved that Ethernet-APL supports high-availability safety applications in conjunction with PROFIsafe. The infrastructure, consisting of cables and field switches, can also be used in safety-relevant installations as a black channel – only field devices and controllers have to support the security protocol.
How does Ethernet-APL fulfil measuring and control tasks as well as functional safety requirements?
Ethernet-APL makes it possible to create uniform digital communication infrastructure, which fulfils measuring and control tasks as well as functional safety requirements. The technology allows sensors and controllers to communicate directly, without the need for conversions or separate systems. The uniform and consistent communication also offers benefits in the form of reduced maintenance requirements: Device management is simplified and devices are easy to replace based on application profiles in the event of an error. With PROFIsafe, safety-relevant data can be transmitted via the same infrastructure as the process data. This simplifies planning and reduces maintenance requirements, as there is no longer a need for separate systems for process control and functional safety.
The first few instances where Ethernet-APL has been implemented in safety-critical applications show that the technology works in practice and meets high safety requirements. Ethernet-APL is already certified for SIL 3 applications in conjunction with PROFIsafe, which further elevates the trust in the technology.
The "Security and PROFIsafe for PROFINET over APL" working group, newly established in early 2025 under the leadership of PI and NAMUR, has set itself the task of conducting a large multi-vendor field test. The aim is to evaluate both new security features in PROFINET and the safety functions of PROFIsafe in detail. Until the multi-vendor field test is completed in late 2026/early 2027, various plug-fests will gradually verify specification-compliant integration. Currently, 40 companies, including R. STAHL, are actively involved in the working group.
From analogue 4 to 20 mA technology to digital Ethernet-APL communication
Although the switch from 4 to 20 mA technology to Ethernet-APL requires the existing infrastructure to be adapted, this is simpler than it seems. Ethernet-APL is compatible with some existing types of cable infrastructure, which reduces the costs and complexity involved in the changeover. What’s more, many of the new devices are backwards-compatible, meaning that existing technologies can continue to be used. By reducing the cabling, integrating the power supply and data transmission into the same cable and enabling the use of additional digital information, significant savings on the planning, operating and maintenance costs can be made in the long term.
Conclusion
Ethernet-APL is a key enabler of the industrial Internet of Things, as it makes consistent digitalisation of the field level possible. It supports modern communication protocols like PROFINET or OPC UA, therefore opening up more options for analysis and diagnostics. This improves not only the efficiency but also the transparency and controllability of processes in real time. Companies who use Ethernet-APL benefit from higher data availability, lower operating costs and simpler maintenance.
Further Reading:
These articles might also interest you
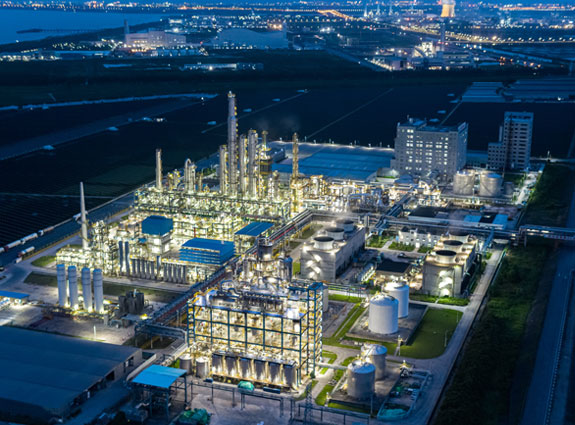
Write new comment