Intrinsically safe circuits require verification and documentation of their intrinsic safety in accordance with the installation regulations set out in IEC EN 60079-14. In practice, however, there are many potential errors to avoid in this process. Avoid the five most common errors that occur in practice.
1. The combination of internal capacitances (Ci) and inductances (Li) has not been observed
In order to prove intrinsic safety, you must compare the output parameters of the source with the input parameters of the consumer. As a general rule, the output values for the voltage, current and power must be lower than the input parameters. The values for the maximum connectable capacitance Co and inductance Lo for the source must be greater than the total of the values for the internal capacitance Ci and internal inductance Li for the sink and those for the cable. This approach, however, is only applicable as long as the following condition is met: Ci = 0 (or negligible) and/or Li = 0 (or negligible).
If this condition is not met, a number of options are available:
- The manufacturer of the intrinsically safe source has certified additional values for the connection of consumers with combined capacitances and inductances. As a rule, a table with several pairs of values for Co and Lo will be provided in the operating instructions or the EU/EC Type Examination Certificate.
- You can use the "50% rule". This procedure is described in EN 60079-11. It initially enables the use of the maximum Co and Lo values, provided that the following condition is met: Li < 1% of Lo or Ci < 1% of Co. In other words, in these cases users can act as though Ci or Li is equal to zero. If this condition is not met, you can halve the values for the maximum permissible capacitance Co and inductance Lo and thereby prove intrinsic safety as usual.
- IEC EN 60079-25 presents a graphical solution that, as a general rule, is used to interconnect non-linear sources. This method can also be used in this situation. However, the standard restricts the application of this method to Ex ib electrical circuits.
- R. STAHL offers proof of intrinsic safety as a service. We can take on the work of reviewing the data and creating documentation.
2. The proof of intrinsic safety has forgotten to consider the cable as a potential energy store
When proving intrinsic safety, the values for the capacitance and inductance of the cable are forgotten when comparing the values. However, cables are potential energy stores! The value is calculated using the capacitance and inductance per unit length for the cable and the length of the cable. If intrinsic safety cannot be successfully proven, there are two potential options:
- Use of the parameters that have been specified by the manufacturer of the cable. These parameters are generally lower than the values specified in the standard of 1 mH/km and 200 nF/km.
- Check whether the requirements for explosion group IIC have been met. If IIB is sufficient, the significantly higher limiting values for C and L corresponding to this explosion group can be used.
3. A simple apparatus has not been assessed
Not all components need to have an EU/EC Type Examination Certificate for use in intrinsically safe circuits. Items known as simple apparatus are excepted from this rule. These items of equipment can be identified by their simple structure, which can be assessed by the user. A simple apparatus must not affect the intrinsic safety of the electrical circuit.
The standard IEC EN 60079-11 sets out three types of simple apparatus:
- Passive components, e.g. switches, distribution panels, resistors and simple semiconductor components
- Energy stores made of individual components with precisely specified parameters
- Energy sources, such as thermocouples, that generate no more than 1.5 V, 100 mA and 25 mW
These simple apparatus also need to be assessed and the results must be documented.
IEC EN 60079-11 and 60079-14 describe how to handle simple apparatus in detail. There are a few points that are particularly important to note:
- Check whether you can fully assess the structure of the device/component.
- Check whether the device/component corresponds to one of the basic types listed above.
- Determine the maximum surface temperature.
- Check the creepage distances and clearances and check whether the IP protection is suitable for the application. In the event of moisture ingress, the creepage distances and clearances are no longer able to fulfil their function.
- Check whether the enclosure surface is suitable with respect to electrostatic charge. You can find information on this subject in IEC EN 60079-0.
- Document your assessment using data sheets and test reports.
Important: Since a non-certified device is being used, any design changes may lead to the regulations for simple apparatus being breached. In the event of a repeat order, this can mean that one or two years later, the assessment is no longer valid. The assessment should therefore be tailored as closely as possible to a period of time or to the version of the component, e.g. its serial number. It is often more practical to use a device or component with an EU/EC Type Examination Certificate instead of verifying that a component is a simple apparatus.
4. When selecting the Pi value, the ambient temperature/temperature class have not been considered
Many intrinsically safe field devices are certified with a selection of Pi values, which must be applied depending on the ambient temperature and/or the intended temperature class for proof of intrinsic safety. It must be ensured that the correct Pi value is chosen. Otherwise, there is a risk that the surface temperature of the device will exceed the temperature class of the surrounding explosive atmosphere.
5. An Ex i consumer with an additional output parameter is used
What's wrong with that? When interconnecting 4-conductor transmitters (with a 4 to 20 mA interface and separate power supply) using galvanic isolators, the Ex i isolator may feature a value for Uo alongside the input parameters Ui, Ii and Pi. This means that a simple interconnection with just one source becomes a complex interconnection with two sources. The following solutions are available:
- It is easiest to use a galvanic isolator, which is specially designed for this application and has suitable parameters (without output parameters).
- A solution that requires much more effort is to obtain proof using the complex interconnection. The method for an interconnection of exclusively linear sources is described in IEC EN 60079-11. The procedure for an interconnection of non-linear sources is set out in IEC EN 60079-25.
Further Reading:
These articles might also interest you
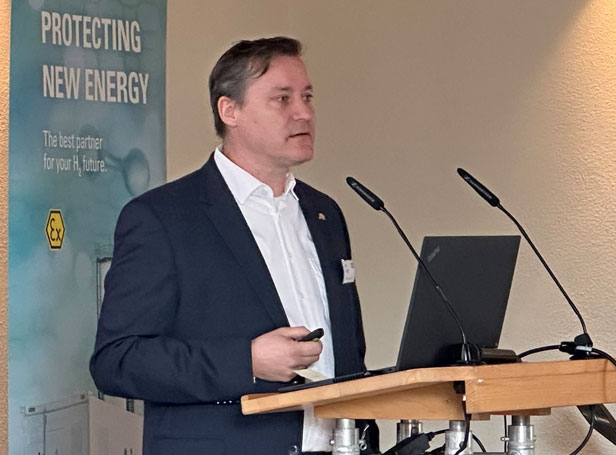
Write new comment