How to meet the requirement of the EU's new ESPR for a digital product passport?
There's no avoiding the controversial topics of digital twins, digital nameplates and digital product passports in industry. Discussions are gaining momentum, especially with regard to the changes heralded in by the EU Regulation (ESPR). The combination of digital nameplates with digital twins not only meets regulatory requirements; there is also huge potential for savings and greater efficiency along the entire value chain, particularly when using digital twins based on asset administration shells.
The EU's future Ecodesign Directive is already making huge waves. The reason? The new ESPR (Ecodesign for Sustainable Products Regulation), which is set to enter into force as early as 2026, goes much further than the EU Ecodesign Directive which has applied since 2009. Until now, the focus was on a product's energy consumption but that is all set to change. What matters now is the sustainable design of products. The aim is to achieve climate neutrality, create a circular economy and make products easier to repair and recycle in order to protect the environment. From the manufacturer to the recycler, a great deal of information about the product's characteristics has to be passed on, which is why the ESPR calls for the introduction of a digital product passport (DPP). The basic idea behind this is that a quick scan using a mobile phone is all it takes for the QR code on the product to link to all of the information contained in the DPP. The DPP therefore has to provide a wealth of information about the service life of products, including their composition, origin and recyclability, as well as details of the materials used, energy consumption and environmental impact. And this is where the combination of digital nameplates and asset administration shells (AAS – according to IEC 63278-1) comes into play.
Even from the very start of industrialisation, traditional printed rating plates have been used as an important central source of information for identifying and documenting products and machines. They make clear identification possible through details such as the manufacturer's name, model and serial number, provide technical specifications for safe operation, document compliance with industrial standards, and help with machine maintenance and inspections. But these rating plates clearly can't meet the increasing requirements associated with a product passport because they are static, are only visible when you are near them, and offer limited space for information. So the time has come for digital nameplates according to IEC 61406: They allow global access to the relevant product or machine data and make it easier to document changes over the life cycle of the components and systems – a key requirement for the industrial Internet of Things.
Combination with the digital twin ensures efficiency
As a more advanced version of the traditional rating plate, the digital nameplate links to all of the information and markings required for the sale, transport and safe use of products in digital form. Standard IEC 61406 defines the digital nameplate as a QR code, 2D data matrix code or tag which clearly identifies an asset (component or system) using a URL. This combination of serial number and manufacturer link is the only one of its kind in the world – it can be used to clearly identify an asset. At the same time, all information and versioned documents associated with a serial number can be called up using it.
The link usually takes you to a website – or, in the case of R. STAHL, even straight to the product's digital twin. R. STAHL's digital twin platform is used to provide up-to-date information in multiple languages all over the world. This makes it possible for operators to boost the efficiency and reliability of systems, to plan maintenance tasks more effectively and to have all relevant documents ready to hand at all times. The interoperable content of the asset administration shell helps ensure compliance with safety and environmental regulations and permits access to all relevant versioned documents.
But that's not all – the asset administration shell is constantly evolving. It ensures that data gathered throughout the life cycle of a system, machine or component isn't lost but is available when the user needs it. And when paired with the previously used software and asset management solutions, this can largely be done automatically. The combination of digital nameplate and a digital twin based on an asset administration shell is particularly efficient. Asset administration shells are data models that are described in manufacturer-independent specifications. The Industrial Digital Twin Association (IDTA), an organisation bringing together over 114 companies, associations and universities, has been instrumental in their development. The IDTA has set itself the objective of establishing the asset administration shell and further developing and standardising submodels. Asset administration shells impress as data models thanks to their exceptional interoperability in particular. The use of classifications such as ECLASS makes it possible to easily import all information into software environments, such as ERP or asset management systems.
The asset administration shell becomes a data hub
Asset administration shells are the data hubs of industry and are essential for efficient data management. These submodels cover various phases of a product's life cycle and are suitable for a wide range of possible applications:
- In engineering, the asset administration shell makes it possible to save and transmit relevant data such as technical data or 3D models, efficiently closing the data gap between engineering and the operating phase.
- It also allows simulation models and the associated data to be passed on.
- What's more, asset administration shells also simplify efficient data transmission in the value chain, from component parts to entire systems, and the integration of this data into ERP or asset management systems.
- Documents can be managed using the handover documentation submodel, which makes automatic integration into document management systems according to VDI 2770 far simpler.
- What's more, machines and smart components can communicate via asset administration shells and request servicing automatically, for example. This meets the requirements of the industrial Internet of Things.
- And that's not all – asset administration shells also make it possible to save all the environmental impacts and material data required by the ESPR/DPP and to pass them on along the value chain in such a way that they are interoperable. This transforms them into a digital product passport.
- And last but not least, asset administration shells can be used in production to make automatic control possible by means of data from configurators.
Major benefits for planners and operators
But how does this actually work in practice? R. STAHL has already used its new digital twin platform in conjunction with digital nameplates for numerous real-life applications. On request, customers can for example be sent automatic e-mail notifications when firmware updates are available – doing away with the need for operators to spend time searching. It is far easier for service staff to access product data. Remote access helps to support technicians in the field – with just a few clicks, maintenance staff in the back office can access the necessary information in the digital twin without having to hunt through paper documentation. The automation of returns processes for the manufacturer's products is another advantage: Return shipping notes are filled in automatically and sent directly to the manufacturer. This reduces mistakes and makes the whole process quicker and simpler.
System operators and maintenance staff also benefit from the creation of a digital maintenance manual through the use of asset administration shells and digital nameplates, doing away with the need for paper documentation in the field. The direct identification of successor products in service cases also significantly increases efficiency and reduces downtimes. For audits and customs processing, all of the necessary documents and certificates can be accessed straight away by simply scanning a QR code on the product, doing away with the need for the time-consuming searching that would usually be required.
To sum it up: The examples show that the digital nameplate in conjunction with the digital twin based on the asset administration shell is an efficient solution for industry in order to meet the demands of the future ESPR and, in particular, to comply with the requirement for a digital product passport. Machine and system builders, as well as device and component manufacturers, are now able to pass on and use data regarding the environmental impact (including the carbon footprint) and sustainability of products along the value chain such that it is interoperable. Users not only benefit from this data, but also from a continuous flow of information which helps to greatly increase efficiency, from engineering and operation through to decommissioning of a system.
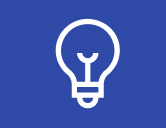
From the ESPR to the digital nameplate
Further Reading:
These articles might also interest you
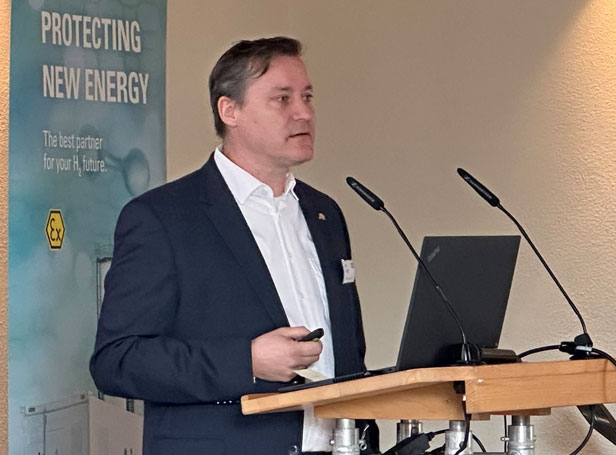
Write new comment