Enabling compact designs, remarkable energy efficiency and a long service life, LED luminaires are also very robust. Based on this combination of features, they are almost universally suitable for use in industrial environments around the world. However, extreme temperature conditionsrequire special design considerations, lest excessive heat or very cold sub-zero environments have a severely negative impact on the lifespan of LEDs. Rico Schulz, Product Manager Lighting Technology at explosion protection expert R. STAHL, discusses the issue of temperature resistance.
Mr Schulz, LED lights are commonly regarded as particularly vulnerable to high temperatures. How much heat is too much for these devices?
Since LED are semiconductor devices, the various temperature-dependent parameters to consider include forward voltage, wavelength and light output. It is not so much the lifespan of the LEDs themselves that is compromised, but rather the integrated control electronics. Because LED chips, drivers, and electronic ballasts are thermo-sensitive components, thermal management is an important factor in luminaire design. The current crop of high-quality LED light fittings easily handles temperatures up to +60 °C. Things become critical if there is extreme heat in excess of +70 °C.
What can drive temperatures up?
Power dissipation caused by the LEDs themselves is a major contributing factor. What is crucial is the temperature at the p-n junction of the integrated chips, which is commonly noted as Tjunction (Tj). Since approximately 70 to 80% of the energy spent on making the light shine is converted into heat, the chip can quickly heat up to temperatures above +100 °C while in use. In the long run, this will severely affect the lifespan and light output of the luminaire.
According to a rule of thumb, a temperature exceeding the permissible maximum by 10 °Cwill cut the lifespan in half. In addition, LED technology is a driving force behind the construction of smaller and smaller, super-compact luminaires. Such designs obviously also shorten the thermal path to the electronics. However, thanks to optimised control electronics, high-end products like our 6036 series LED tubular light fittings now provide far better temperature stability.
How much of a role does the ambient temperature play?
Depending on the type of application, LED fittings can of course be exposed to relevant environmental temperatures – for instance, in machine and systems engineering when they are installed in generators. Such luminaires therefore require a particularly heat-resistant design to weather temperatures exceeding +70 °C.
And there are also geographical extremes that really test their durability. In process plants in Middle Eastern deserts, housings may heat up to well over +60 °C, especially in direct sunlight. For operation in such locations, the housing materials and gaskets must be designed to permanently withstand intense heat and especially extreme temperature fluctuations. Other environmental stress factors, such as high humidity or ultraviolet light, further add to the requirements.
Are thermal issues taken into account for enclosure construction?
In fittings equipped with conventional fluorescent lamps, air acts as a thermal insulator. For this reason, fluorescent tubes should be installed in housings with a large air volume to keep the surface temperature low. With LED lights, the effect is just the opposite. They require heat to be dissipated on the outside as quickly as possible. However, since air is a poor conductor of heat, the enclosures for these products should be designed as compact as possible to minimise the volume of air. This is the idea behind the development of LED tubular lights.
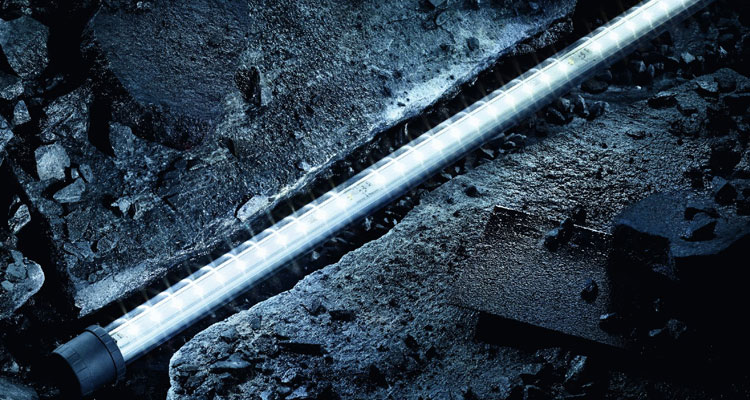
What deserves particular attention with regard to thermal management?
Thermal management seeks to achieve the most effective heat dissipation through conduction and convection. Optimal heat transfer is best realised through direct physical contact between components, so that the dissipated heat can transfer from the junction through the LED housing and into the luminaire body or heat sink. For unobstructed heat dissipation, there should be no air gaps or pockets along the thermal conduction route. Convection then ensures that heat is dissipated via the external surface of the fitting into the surrounding atmosphere. Large surfaces and free air circulation are obviously helpful for quick heat dissipation by convection.
How can intelligent power electronics reduce temperature stress?
Fine tuning between LED light sources and electronics is crucial to find the optimal balance between performance, lifespan and thermal stress. Even the most intelligent electronics cannot completely prevent thermal leakage power. Using sensor input, however, they can respond to system temperature and reduce power consumption to ensure the designated lifespan of the system is not compromised. In addition, state-of-the-art power electronics are highly efficient and consume less than 6% of the total output as power loss.
Our new 6125 and 6525 series LED floodlights are a good example – they provide a maximum luminous intensity of more than 80,000 cd at 225 W. Conventional floodlights equipped with gas discharge lamps achieve about 30,000 cd maximum luminous intensity using 400 W power input. Compared to these, the LED fittings are not only much more efficient and light weight, but also feature a very low-maintenance, very durable design.
What else can be done to cool LED fittings?
For powerful luminaires in the 150 W range and above that generate a lot of heat, cooling fins on the exterior are an option to increase the surface for heat dissipation. However, this can cause other problems in harsh industrial environments with a lot of dust or dirt. Dirt that accumulates between such fins again reduces proper heat dissipation and may require extra cleaning routines.
Active cooling via integrated fans is another option for light fittings. However, the necessary redundancy makes this a time-consuming and expensive solution especially in hazardous areas.
Speaking of cooling: do LED lights ever get "cold feet", too?
In principle, LEDs like it cold – moderately cold, that is. At very low temperatures below -50 or -55 °C, which can occur in Arctic regions, the luminaires are exposed to high levels of mechanical stress as they heat up in operation. This is detrimental to frost-sensitive components. EMC protection also suffers. For this reason, luminaires for such operating conditions also require a special design that mitigates the temperature difference, e.g. via intelligent circuitry.
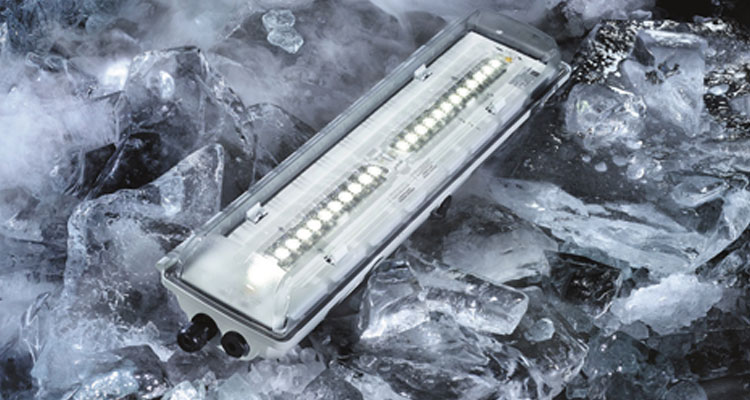
How do you test and rate temperature susceptibility?
Besides consulting temperature resistance calculations, we perform various stress tests together with our partner companies. For instance, in order to determine vulnerabilities and exposure limits as early as possible during product development, we subject our equipment to an accelerated ageing process in accordance with HALT (Highly Accelerated Lifetime Test) provisions. As part of this procedure, the luminaires are exposed to rapid temperature changes and vibrations in a climatic test chamber. The failure rates of the critical elements are determined to define the life expectancy within the permissible temperature range.
Because LEDs, compared to other light sources, do not fail suddenly, but emit less and less light over time, their end-of-life is defined as a degradation of the luminosity to 70% of the initial value.
Can you give us an outlook on future developments?
LED technology is now already very sophisticated. Efficiency values greater than 200 lm/W are already safely achieved by several manufacturers.
Current development potential lies more in colour rendering values. Here, a trend towards higher values is emerging, which can be attributed to a technological advancement of the conversion material. Coming from an average colour rendering of around 70, the current status is colour rendering values greater than 80 for standard applications. Soon, values above 90 will be common and provide a decisively better quality of light.
Also there is a trend towards further optimisation of intelligent control electronics to make the devices even more efficient, economical and fail-safe.
Further Reading:
These articles might also interest you
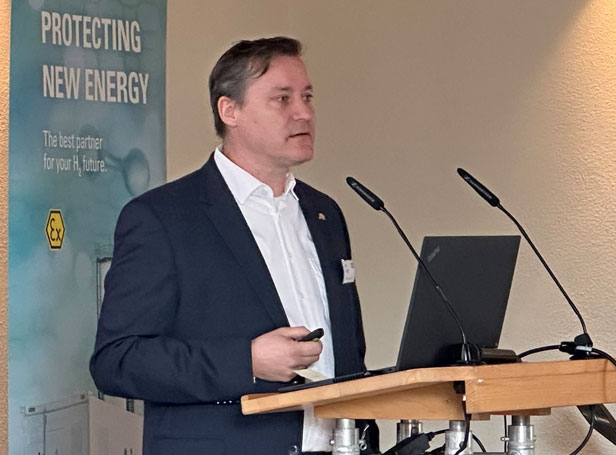
Write new comment