Most seagoing vessels are big polluters. But things have been improving for a long time. LNG engines significantly reduce emissions of sulphur dioxide, nitric oxides and particulate matter. The necessary LNG FGSS (fuel gas supply systems) offer a high level of safety. By choosing this technology, shipowners are investing in the future.
Who would have thought it? Around 70% of all goods (in terms of tonne-kilometres) are transported by sea. That is a huge quantity. Transport is dominated by cargo ships, bulk carriers, tankers and container ships. The more than 90,000 ships travelling the world's oceans include over 7000 passenger vessels. Their number is growing rapidly. Almost all of them, without exception, are powered by combustion engines, the majority with heavy fuel oil. It will therefore come as no surprise that they have a huge impact on the environment. Alongside oil pollution in oceans, greenhouse gas emissions are particularly harmful to the environment. The IMO (International Maritime Organization) estimates that the CO2 emissions generated by shipping in 2012 accounted for around 2.2% (around 3% according to more recent estimates) of global emissions caused by humans. It expects this figure to rise by 50 to 250% by 2050 unless any preventative measures are taken. That's without considering nitric oxides, particulate matter, soot and sulphur dioxide. This causes serious pollution in ports.
Liquefied natural gas reduces greenhouse gases
Using marine diesel oil (MDO) as a low-sulphur fuel has made it possible to reduce at least some emissions, especially of sulphur dioxide. Using liquefied natural gas (LNG) is another option. This contains no sulphur. Using it also reduces emissions of nitric oxides and particular matter. As long as methane slip is prevented, LNG has a far better greenhouse gas balance than heavy fuel oil or diesel. LNG should be considered as a fuel, especially in particularly fragile marine areas (SECA zones).
It is therefore an obvious solution to power tankers which transport LNG with liquefied natural gas and the boil-off gas that is constantly produced. This has been a reality for more than 50 years. Nowadays, most of the around 600 LNG carriers are powered by LNG. By 2020, this number had grown due to the addition of another 175 LNG-powered seagoing vessels, while many others were already ordered by this point. Eight cruise ships with LNG operating mode now also travel the world's oceans, while countless others are in construction.
Reliable natural gas supply on board
LNG fuel gas supply systems (FGSS) are required for operation with LNG. These are custom designed for different types of vessels – from tankers, bulk carriers and container ships through to ferries and cruise ships – and mostly supplied as a module. Hamburg-based company Marine Service, one of the most important suppliers of LNG FGSS, emphasises that maximum redundancy and availability are important.
The gas supply systems are incredibly complex. The central component is an LNG evaporator. The other main components that make up an FGSS also include pumps and compressors, a water/glycol module, low-temperature valves and superheaters, with some of these components being redundant. In particular, the evaporator itself has to be correctly hermetically sealed and resistant to thermal loads. The system also contains many electrical components, including a PLC-based automation system, which manages the activation of the corresponding redundant component in the event of component failure. This is because the gas supply must be ensured at all times.
Safe regasification at all times
During operation, the LNG is pumped into the evaporator from vacuum-insulated storage tanks using a submersible pump. This uses water/glycol and a heat source on board to convert the LNG in the heat exchange circuit into a gaseous state, in other words to regasify it. A gas valve unit regulates the pressure and volume of the natural gas in order to ultimately transport it to the engine.
It goes without saying that ensuring the safety of the equipment and the vessel at all times, as well as of the personnel and any passengers on board, is of the utmost importance. A crucial element of the safety equipment is a safety valve, which dumps natural gas into the atmosphere in the event of a pressure rise.
Explosion protection with pioneering systems
Safety is the top priority when it comes to regular regasification too. Explosion protection solutions like the ones offered by R. STAHL play an important role here. Firstly, explosion protection should be incorporated into the design to prevent gas leaks or, at least, to stop an explosive mixture of natural gas and air forming. However, since this can never be completely ruled out, stage 2 of the safety concept takes effect: Electrical explosion protection. Sparks and hot surfaces must not supply so much energy to an explosive mixture which forms under certain circumstances that it explodes.
Suitable explosion-protected and appropriately certified technology prevents this from happening. It must be approved for explosion group IIA and temperature class 1 when operated with natural gas. This applies, for example, to measuring instruments, operating elements and indicators, as well as to control systems like the IS1+ Remote I/O system from R. STAHL. It has proved to be successful on many LNG tankers and other LNG-powered vessels. It also meets additional requirements for shipbuilding, such as increased immunity to the ship's radio and vibrations and a wide operating temperature range from -40 °C to +75 °C.
Diagnostics and redundancy for maximum availability
System solutions based on IS1+ include cabinets specially tailored to the application with the other required components, like operating elements. Modern remote I/O systems which are suitable for Zones 1 and 2 do away with the need for I/O cards or Ex i isolators, among other components. What's more, fewer copper cables than usual are required. This solution therefore reduces weight and saves space, which pays off on vessels in particular. The integrated diagnostics also provide a warning of failures. This increases availability. This is also ensured by various redundancy options, such as those for the CPU and the power module.
The necessary ship approvals are, of course, another requirement resulting from marine applications. IS1+ possesses these approvals which, together with its international approvals for Zones 1 and 2 and Divisions 1 and 2, makes it the world's mostly frequently used remote I/O system. It can be used in virtually any automation system.
With LNG, shipowners are looking to the future
With reliable and safe automation, engines running on LNG, which is the most environmentally friendly marine fuel available at present, will give rise to future-proof solutions even if environmental regulations for shipowners and users are made even more stringent. Various ship classification societies issue an AiP (approval in principle) certificate for the design of an LNG-powered ship; this is equivalent to basic approval. An investment in long-lasting technology for FGSS, like that provided by R. STAHL, will pay off quickly, allowing shipowners to remain competitive in the long term.
Further Reading:
These articles might also interest you
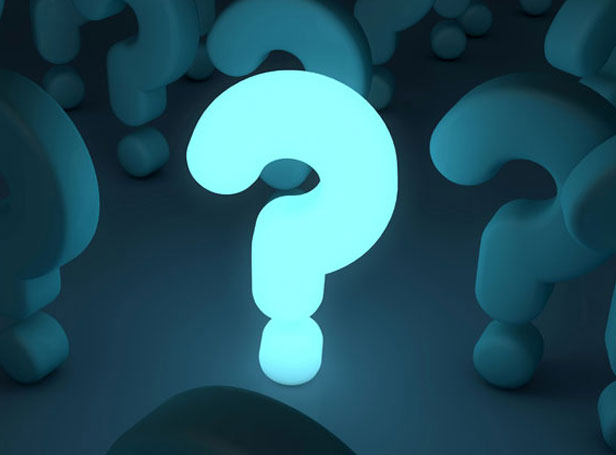
Write new comment