John Zagame is responsible for the R. STAHL business in Australia in one of the most important LNG export markets. The lessons he has learned could be exceedingly useful for current projects across the globe. He can put a concrete number on the cost to users when investment costs for products in the "hot work" area in LNG plants are prioritised over long-term reliability and maintainability. He has a few tips for project planning too. He is convinced that LNG will be produced beyond 2050 and, alongside hydrogen, will play a significant role for a long time yet in liquefied energy sources.
Mr. Zagame, what importance do you attach to LNG as an energy source worldwide – in the short term and medium term?
John Zagame: LNG and natural gas is perfectly positioned as a transitional fuel towards meeting our immediate needs in the short to medium term for energy, and at the same time heading towards a lower emissions target or eventually a zero emissions target in the future. It plays a critical role in the short term, particularly to support growth in economies in developing nations. We're seeing opportunities for populations to grow into a greater middle class. The importance of natural gas, or LNG in its liquefied form, helps growth and prosperity. There's also a large push from many countries around minimising coal and oil consumption – amongst other things by turning towards natural gas. We are also seeing the use of LNG in the production of blue hydrogen through electrolysis of water. Both liquefied natural gas and liquefied hydrogen have a role to play in providing an energy source which is transportable and storable.
From 2040 to 2050, many industrial nations want to have mastered the revolution in power supply to such an extent as to achieve greenhouse gas neutrality. Will LNG still have a reason for being after that?
John Zagame: LNG will surely have a longer-term role to play beyond 2050 too. Some studies show that the production of LNG in Australia by 2050 will still be a rate above what it is today. There is talk about 13 to 15% above the rate of production today. As each of the economies grows globally, there'll still be a demand for energy that is transportable and cleaner than oil and coal, even in 2050. There'll still be a role for LNG in the production of specialty chemicals and blue hydrogen. Change is afoot in shipbuilding too. There's a large push towards moving shipping propulsion from heavy oil to cleaner options such as LNG. It's an obvious choice for LNG carriers in particular, but even for other shipping as well.
How is Australia currently positioned on the world market for LNG energy? What developments do you expect to see for the LNG energy production markets?
John Zagame: Australia is now exporting around 80 million tons of LNG per year. Now we have five LNG projects operating in western Australia, three in Queensland which is on the east coast, and two in northern Australia. In the last ten years, almost 200 billion Australian dollars, which is about 120 billion euros, have been invested in LNG in Australia.
So Australia is a large supplier on the global LNG market. Australia recently overtook Qatar as the largest producer of LNG globally. That could change soon because there are some large LNG projects in production at the moment, like the north field expansion project in Qatar. This will almost double natural gas exploration in Qatar. There are also large projects in the USA, such as the Rio Grande project in Texas. There are some LNG projects in Africa. The development of the Arctic LNG project in Russia is uncertain.
The energy crisis that has occurred because of the conflict between Russia and Ukraine could accelerate the demand for some of these projects or expansion of projects. Furthermore, some of the LNG trains globally are still not operating at a hundred percent name plate capacity; increased operational efficiency would result in greater opportunity for growth. Given the demand and with high prices now, there's more incentive to exploit this.
In many countries, there is certainly increasing demand for LNG. New terminals and regasification units currently being built. What can planners and future operators of LNG plant infrastructure learn from the Australian experience?
John Zagame: A lot was learned in Australia. A number of massive projects all being developed concurrently put a huge demand on supply chain for the critical equipment to go into those projects and put a huge strain on experienced manpower capacity. For example, gas compressors, which we used for the liquefaction lines, were in short supply. It had an inflationary effect on costs. More modest scalable investments are now more attractive to global or national oil and gas companies. Care is taken to ensure that critical supply chains aren't overwhelmed. Lead times of one to three years now mean that projects can be developed in a more orderly fashion, not exceeding capacity limits from suppliers and from the manpower. It's just a matter of planning. Australia is one of those world's largest LNG exporters; we therefore don't have any experience with regasification in Australia. But our basic experience with large projects is transferable.
Is it possible to put a number on how many LNG plants R. STAHL has been involved in, from liquefaction to regasification?
John Zagame: The total number globally is really quite difficult to find out. It's ten or more already in Australia. A large proportion of our products go into the major EPCs; we don't always know what they are intended for. When I'm engaging with the EPC, I always try to establish the functional requirement specification and the detailed design. This is because then there will be compatibility when it comes to integration of systems from R. STAHL, as well as ensuring common spare parts and common maintenance plans. From our experience, it can save the end customer a lot of time and a lot of money if they can detail a design up front, which R. STAHL can help with. It ensures a more streamlined delivery, installation and integration. R. STAHL can draw on over 40 years of experience; that's how long we have been involved in LNG projects.
R. STAHL has certainly gained valuable experience over those four decades. What lessons learned for explosion protection in LNG system can you share with us?
John Zagame: In my view, ensuring long-term reliability and maintainability is the most important thing. Once the plants begin to operate, it is very difficult to gain access. Hot work requires a lot of risk management as there are explosive gases in the area. This increases the costs for repair and maintenance. Also, some of the equipment is installed locations that are very difficult to access. If we have a luminaire on an offshore production platform, for instance, according to the information I have, it can cost several thousand dollars just to gain access and to repair and maintain it. So it's worth thinking about the long-term reliability and minimal maintenance requirements and selecting the best product to serve in each application. Sometimes, planners focus on the acquisition costs and not on the long-term lifecycle costs.
Another piece of advice is simplified designs and best use of stock items. Sometimes, the people doing the design or specification request products outside of our standard product line items which could provide a minimal improvement in operation. That affects the availability of spare parts, often with additional training required for maintenance personnel. Against this backdrop, it is often better to stick to our standard production lines and utilise what is normally available as a stock item in the destination country – not the country that is doing the design or where the EPC or OEM machine is being built.
Where new LNG infrastructure is being built today, there is often talk about the need to design it to be "hydrogen-ready" to facilitate an easy switch to green hydrogen. What do you think of that?
John Zagame: When the new LNG plants went into operation here in Australia in 2015, there wasn't a lot of discussion around building hydrogen-readiness into those plants. But in many ways, you can say that hydrogen is becoming the liquid fuel of the future. Hydrogen requires different equipment to LNG in some cases for the hazardous area. Redesign for hydrogen will therefore require refitting of infrastructure. Nowadays, it is much better to design in capability for operating within a hydrogen environment for new LNG plants, even if it does require some additional upfront costs. You can already see that some of these turbo machineries eventually will be operating with hydrogen. It will help to reduce the emissions as part of the LNG production process.
How does R. STAHL's product range for the LNG sector differ from other supplies of explosion-protected technology?
John Zagame: R. STAHL is considered the number one hazardous area manufacturer in the industry. There is a lot of trust, which has been built on our extensive experience and the leadership that we've brought to the industry. We have set the standards by which others follow when it comes to trustworthy design for the sector. We focus on the hazardous area. We also have the broadest range of products in the sector, everything from lighting, installation control to our systems and automation products and even our services. With our services, we provide end-to-end lifecycle support for our customers. That's what differentiates us from other suppliers: We look at everything from design to end of life.
Are there products that R. STAHL has developed specially with a focus on use in LNG plants?
John Zagame: Our products are very suitable to LNG applications in general. We did some really groundbreaking work in redeveloping new technology for LNG. For one of the big projects we did in Australia, we built a lot of transformer panels, which were very unique in design. They contributed towards reducing the amount of expensive cabling that the customer had to install in these plants in order to achieve the functionality they wanted out of the plant. Our remote I/O technology can also reduce the amount of cabling and installation complexity. This is particularly useful when there are a lot of OEM balance plant modules being built in all different parts of the world, but coming together as one part of an overall system design. Use of remote I/O and intelligent networking simplifies the system integration and therefore the cost of cabling, installation and start-up. Specific adaptation of our panels and distributor cabinets for LNG liquefaction plants provide the customer with significant advantages. Our customers have recognised R. STAHL's potential for innovation. That's why we have been and are still so successful in winning a lot of large LNG projects. Our LNG-specific products fulfil the requirements completely.
What LNG projects from the past ten years were important in your opinion?
John Zagame: When you've got children, it's always hard when someone asks you which one is your favourite child. I love all my projects (laughing). I have some sentimental attachment to some of the older "children". I can't mention any names, but one is one of the large projects in west Australia. LNG liquefaction plants were being built with some of the biggest gas compressors ever built in the world. We supplied plugs and socket panels, power distribution panels that I mentioned, light fittings, control stations, terminal boxes in stainless steel, emergency light fittings, as well as luminaires and control panels. The project itself comprised two parts: The main liquefactions plants and the LNG trains that were operating there, as well as the storage tanks. Again, with the storage farm, we provided control stations, emergency fluorescent luminaires, GRP grounding monitoring devices, other lighting fixtures, switching sockets and terminal boxes, all in stainless steel. So it was a huge amount of equipment, which was delivered over a three- to five-year programme. The project went exceptionally well in very arduous environments with a huge amount of UV and high temperatures. The amount of UV was so great that it can impact certain products if they're not built to work in this environment. We're very proud of that project, for which we were able to service a lot of short-notice "field requests", even though the location was very remote. It's a bit like being on a different planet.
Do you have another "favourite child"?
John Zagame: There are actually three, namely three export LNG liquefaction plants on Australia's east coast, on an island off the city of Gladstone. Although these three plants are all separately owned, they were built at the same time. There were huge demands on R. STAHL production and logistics for the equipment required to be delivered on time for everyone so that the plants were able to be commissioned on time. These three plants were completed in 2015. R. STAHL once more proved its capabilities.
Profile: John Zagame
Further Reading:
These articles might also interest you
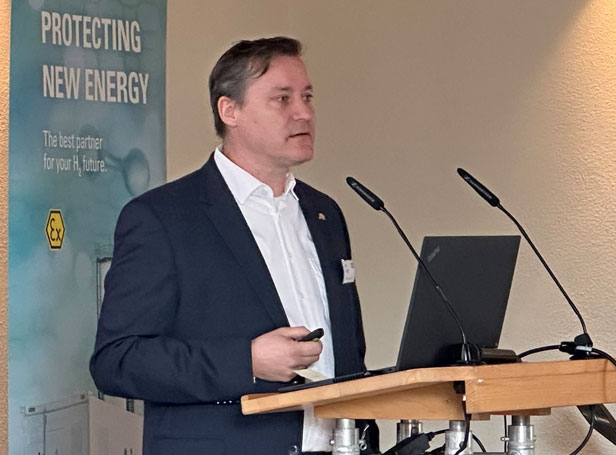
Write new comment