If, despite implementing primary explosion protection measures, you are unable to eliminate the possibility of an explosive atmosphere forming, secondary explosion protection measures must be taken. This refers to avoiding effective sources of ignition.
Typical sources of ignition
Typical sources of ignition according to EN 1127-1 include:
- Hot surfaces
- Flames and hot gases
- Mechanically generated sparks
- Electrical installations
- Electrical compensating currents
- Static electricity
- Lightning
- Electromagnetic fields
- Optical radiation
- Ionising radiation
- Ultrasound
- Adiabatic compression
- Chemical reactions
All sources of ignition will always generate energy, either in the form of heat or in the form of sparks. The sources of ignition are assessed based on the likelihood of an explosive atmosphere forming.
Gas | Zone 0 | An area in which a hazardous explosive atmosphere as a mixture of air and combustible gases, vapours or mists is present continuously, for long periods or frequently. |
Zone 1 | An area in which a hazardous explosive atmosphere as a mixture of air and combustible gases, vapours or mists sometimes occurs under normal operating conditions. | |
Zone 2 | An area in which a hazardous explosive atmosphere as a mixture of air and combustible gases, vapours or mists is normally not present, but if it does occur, is rare and persists only for a short period of time, under normal operating conditions. | |
Staub | Zone 20 | An area in which a hazardous explosive atmosphere in the form of a cloud of combustible dust in the air is present continuously, for long periods or frequently. |
Zone 21 | An area in which a hazardous explosive atmosphere in the form of a cloud containing combustible dust in the air is likely to occur under normal operating conditions. | |
Zone 22 | An area in which a hazardous explosive atmosphere in the form of a cloud containing combustible dust in the air is normally not present, or is only present for a short period of time, under normal operating conditions. |
In Zone 0 and Zone 20, sources of ignition that may be continuously, frequently, occasionally or rarely present must be eliminated. In Zone 1 and Zone 21, sources of ignition that may be continuously, frequently or occasionally present must be eliminated. In Zone 2 and Zone 22, sources of ignition that may occur during normal operation of the devices must be eliminated.
Minimum ignition temperature and minimum ignition energy
The minimum ignition temperature and minimum ignition energy of the combustible materials are important parameters to consider when assessing whether sources of ignition are effective or not.
Substance | Minimum ignition temperature in °C | Temperature class |
Hydrogen | 560 | T1 |
Acetone | 527 | T1 |
Ethanol | 400 | T2 |
Carbon disulphide | 95 | T6 |
Examples: Minimum ignition temperature of combustible gases and vapours.
Substance | Minimum ignition energy in mJ | Group |
Hydrogen | 0,016 | IIC |
Acetone | 0,55 | IIA |
Ethanol | 0,28 | IIB |
Carbon disulphide | 0,009 | IIC |
Examples: Minimum ignition energy of combustible gases and vapours.
For instance, hydrogen has an ignition temperature of 560 °C. This means that this substance will ignite on contact with a hot surface if the temperature of the surface is at least 560 °C. In contrast, the ignition energy of hydrogen is very low, which makes this substance dangerous, especially in the vicinity of electrically or mechanically generated sparks.
Substance | Minimum ignition temperature of the dust cloud in °C |
Aluminium dusts | 560 |
Wax dusts | 350 |
Sugar dust | 480 |
Wheat flour type 405 | 400 |
Examples: Minimum ignition temperature of combustible dusts.
Substance | Minimum ignition energy in mJ |
Fine aluminium dusts | < 1 |
Wax dusts | 1-10 |
Sugar and milk powder dusts | 10-100 |
Wheat flour, coal dust | > 100 |
Examples: Minimum ignition energy of combustible dusts.
The ignition temperature of the dust cloud and that of the dust layer must be compared with the maximum permissible surface temperature of the equipment. When doing so, safety factors must be taken into consideration. The maximum surface temperature of the device must only be two-thirds of the dust cloud ignition temperature; similarly, the maximum surface temperature of the device cannot be higher than the ignition temperature of the dust layer minus a safety allowance (75 °C for a 5-mm dust layer).
How should you proceed?
As a system operator, the following process is recommended:
- Firstly, potential sources of ignition, their causes and the likelihood of their occurrence must be analysed.
- Next, measures to avoid ignition hazards must be identified. These must include both technical and organisational measures, which ensure that no sources of ignition can become effective, or that the explosive atmosphere and the source of ignition cannot mix. This must all be documented accordingly.
- If organisational protective measures are not sufficient, explosion-protected devices can be used. These are designed so that sources of ignition cannot become effective. When doing so, you must also bear in mind that specific installation requirements may apply.
It is not always possible to avert an explosion hazard by selecting suitable equipment and implementing organisational measures. In this case, additional explosion protection measures must be implemented in order to control the effects of an explosion.
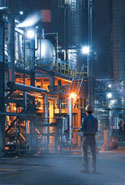
Write new comment