In the chemical and petrochemical industry, in crude oil and natural gas extraction, in mining, in the foodstuff industry, in machine engineering and plant engineering, and in many other branches of industry, combustible gases, vapours or mists can escape during manufacturing, processing, transport and storage – and other processes can generate combustible dusts. These substances can form an explosive atmosphere if they mix with oxygen in the air. If this atmosphere is ignited, this can cause explosions that can result in significant injury and/or material damage.
What is an explosion?
An explosion is the sudden chemical reaction of a combustible substance involving a high release of energy. It doesn't take much to create a big bang:
- Just a combustible substance in the form of a gas, vapour, mist or dust.
- The combustible substance is present in combination with oxygen, or air that contains oxygen. This combination results in the formation of an explosive atmosphere.
- Lastly, a source of ignition causes this atmosphere to ignite.
Explosion protection revolves around preventing these explosions. To do so, you need to prevent the formation of an explosive atmosphere.
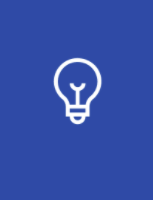
Explosive atmosphere
Stop a big bang before it starts
Protective measures must be implemented in order to prevent an explosion. First and foremost, the formation of explosive atmospheres must be prevented (primary explosion protection). As a result, a check must be performed in order to determine whether the hazardous substance can be replaced with a different substance that does not represent an explosion hazard or minimises the likelihood of an explosion. Frequently used methods include ventilation – ensuring that a room is well ventilated can significantly reduce the concentration of combustible materials.
Furthermore, ways to limit the concentration in the processes can be considered. Adding buffer gases such as nitrogen or carbon dioxide enables you to reduce the oxygen concentration in the process, in order to prevent the formation of an explosive atmosphere.
If explosion hazards cannot be eliminated or can only be partly eliminated using primary explosion protection methods, precautions must be taken to prevent ignition. No effective sources of ignition must arise as a result. In some cases, however, this is not a reliable solution, as certain sources of ignition cannot be eliminated. In these cases, measures that limit the hazardous effects of any ignited explosions to an insignificant extent must be implemented. "Tertiary" or "constructive" explosion protection includes the use of explosion-proof structures, explosion pressure relief, explosion suppression and explosion barriers.
Dividing hazardous areas into zones
In hazardous areas, the frequency and duration of the presence of an explosive atmosphere may vary, which is why these areas are categorised using different zones. This zone classification reflects the probability of the occurrence of an explosive atmosphere. This makes it easier for you to select corresponding devices and design appropriate electrical installations.
Gas | Zone 0 | An area in which a hazardous explosive atmosphere as a mixture of air and combustible gases, vapours or mists is present continuously, for long periods or frequently. |
Zone 1 | An area in which a hazardous explosive atmosphere as a mixture of air and combustible gases, vapours or mists sometimes occurs under normal operating conditions. | |
Zone 2 | An area in which a hazardous explosive atmosphere as a mixture of air and combustible gases, vapours or mists is normally not present, but if it does occur, is rare and persists only for a short period of time, under normal operating conditions. | |
Staub | Zone 20 | An area in which a hazardous explosive atmosphere in the form of a cloud of combustible dust in the air is present continuously, for long periods or frequently. |
Zone 21 | An area in which a hazardous explosive atmosphere in the form of a cloud containing combustible dust in the air is likely to occur under normal operating conditions. | |
Zone 22 | An area in which a hazardous explosive atmosphere in the form of a cloud containing combustible dust in the air is normally not present, or is only present for a short period of time, under normal operating conditions. |
Classifying devices in categories and by protection level
The various safety requirements for the equipment used depend on the probability of the occurrence of an explosive atmosphere. Devices which are used in Zone 0 or 20 must correspond to device category 1G or 1D and have equipment protection level (EPL) Ga or Da. Equipment in category 2G or 2D with equipment protection level (EPL) Gb or Db may be used in Zones 1 or 21. Equipment of this kind that belongs to device category 3G or 3D with EPL Gc or Dc is suitable for Zone 2 or Zone 22.
Zone | Duration of presence of explosive atmosphere | Device category | Equipment protection level (EPL) | |
Gases, vapours, mist | 0 | Continuous, over long periods, permanent | 1G | Ga |
1 | Occasionally | 2G | Gb | |
2 | Normally not present, or only for short times | 3G | Gc | |
Dusts | 20 | Continuous, over long periods, permanent | 1D | Da |
21 | Occasionally | 2D | Db | |
22 | Normally not present, or only for short times | 3D | Dc |
Division into explosion groups and temperature classes
Additionally, devices are divided into groups depending on the substances for which they are suitable:
- Group II
Devices for gas hazardous areas
These are further categorised according to the properties of the explosive atmosphere for which they are suitable – IIA (typical propane gas), IIB (typical ethylene gas) and IIC (typical hydrogen gas).
- Group III
Devices for dust hazardous areas
Depending on the type of dust, the devices must meet the criteria for IIA (combustible lint), IIB (non-conductive dust) and IIC (conductive dust).
Furthermore, equipment must only be operated in hazardous areas if its maximum surface temperature is below the ignition temperature of the surrounding explosive mixture. For this purpose, temperature classes T1 to T6 are defined. In this regard, the maximum permissible ambient temperature must be considered, as this also influences the device temperature.
Maximum surface temperature of equipment in °C | Ignition temperature of gases and vapours in °C | Temperature class |
450 | > 450 | T1 |
300 | > 300 to 450 | T2 |
200 | > 200 to 300 | T3 |
135 | > 135 to 200 | T4 |
100 | > 100 to 135 | T5 |
85 | > 85 to 100 | T6 |
Combustible dusts are not divided into temperature classes. The ignition temperature of the dust cloud must be compared with the maximum permissible surface temperature of the equipment. Since dusts can also accumulate on equipment, the ignition temperature of the dust layer must also be taken into account.
Types of protection for electrical devices in hazardous areas
Only explosion-protected devices may be used in hazardous areas. These can be designed using a range of types of protection. Types of protection are techniques that prevent a device from becoming a source of ignition or transmitting an explosion. Electrical explosion-protected devices can be designed in a range of types of protection, in accordance with the IEC 60079 series of standards:
- Increased safety "e"
Additional measures and an increased level of safety are used to prevent the formation of sparks, arcs or impermissible temperatures, which could act as sources of ignition. - Flameproof enclosure "d"
In this type of protection, the enclosure construction prevents the spread of an explosion. An explosion that occurs inside the enclosure is not capable of igniting the surrounding explosive atmosphere. - Pressurized enclosure "p"
The pressurized enclosure type of protection describes the method used to prevent an explosive atmosphere from penetrating the enclosure due to an overpressure. - Intrinsic safety "i"
Equipment that is used in a potentially explosive area only contains intrinsically safe electric circuits. An electric circuit is intrinsically safe if no sparks or thermal effects are produced under specified test conditions which might result in the ignition of a specified explosive atmosphere. - Liquid immersion "o"
Electrical equipment or parts of electrical equipment are immersed in a protective fluid so that an explosive atmosphere present outside of the enclosure cannot be ignited. - Powder filling "q"
The equipment is filled with fine-grained filler, which ensures that potential sources of ignition, such as arcs or high temperatures, are trapped in the enclosure. - Encapsulation "m"
Parts which may ignite an explosive atmosphere are embedded in sealing compound such that the explosive atmosphere cannot be ignited. - Type of protection "n"
This type of protection ensures that electrical equipment is not capable of igniting a surrounding explosive atmosphere. It can be described as improved industrial quality, which is designed for normal operation under defined operating conditions. - Optical radiation "op"
Technical measures prevent ignition of an explosive atmosphere by optical radiation. - Protection by enclosure "t"
This type of protection is a special type of protection for dust hazardous areas. Thanks to the tightness of the enclosure, dust cannot penetrate at all or the amount which can is limited to a safe level. For this reason, ignitable equipment can be installed in the enclosure. The enclosure's temperature must not ignite the surrounding atmosphere.
The type of protection used by manufacturers for electrical devices is highly dependent on the type and function of the equipment.
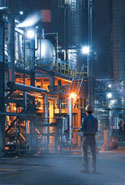
Basic principles of explosion protection
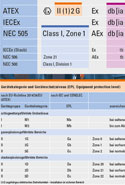
Write new comment