Pressurised enclosures for explosion protection
Capitalising on R. STAHL's expertise in the field of explosion protection, Saxony-based plant manufacturer Andreas Junghans built a filtration test system for use in hazardous areas. The incredibly compact system is mounted on a frame with casters, which means it can be used in different locations in line with the customer's requirements. An inert gas is flushed through the switch cabinet to create a non-explosive atmosphere. The enclosure itself is protected by a pressurised enclosure, which allows the entire control system to be equipped with inexpensive standard industry components. The operating terminal is an open HMI with an R. STAHL touchscreen.
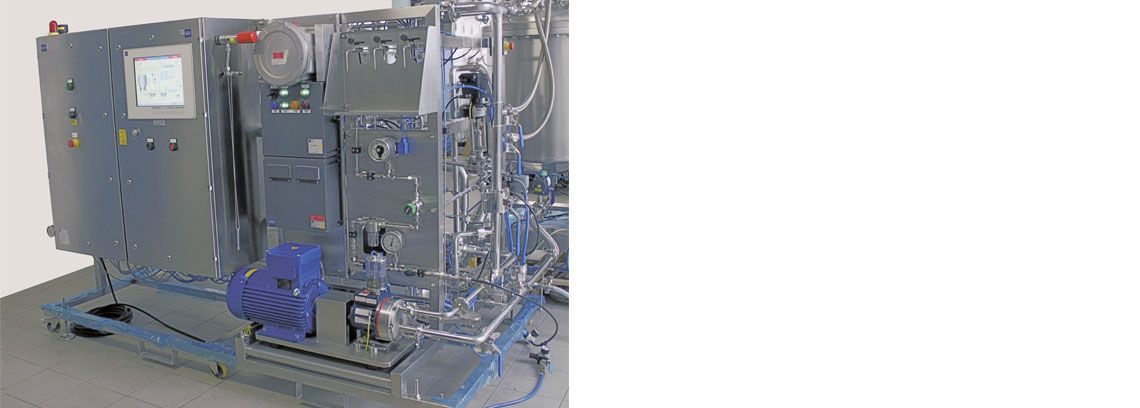
Application
Apart from the explosion protection requirements, the nanofiltration system also had to comply with the GMP (good manufacturing practice) guidelines, have a maximum operating pressure of 60 bar, and be easy to move to different operating locations. This is why the system was designed to be incredibly compact, and is mounted on a frame with casters along with the switch cabinet.
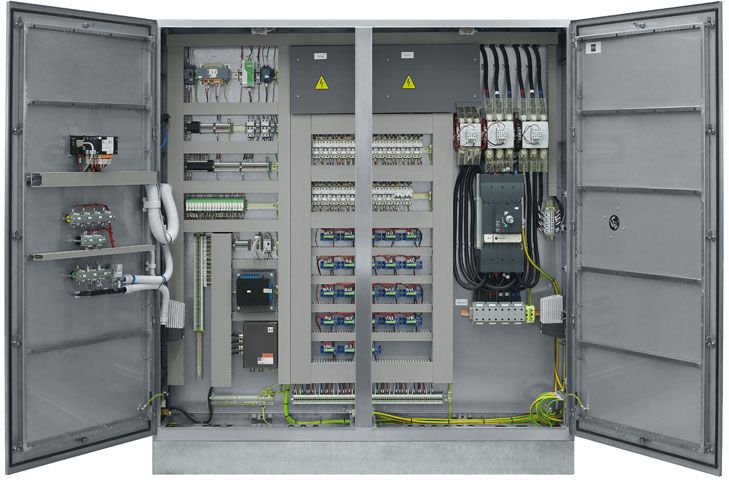
Ex p switch cabinet
As the system was a one-off production for use in hazardous areas and the design of the control system was to correspond to that of control systems used in non-hazardous areas and comprise standard components, the pressurised enclosure (Ex p) type of protection was chosen for the switch cabinet.
Inside the Ex p enclosure, a non-explosive atmosphere is created by flushing an inert gas through it and generating an overpressure of a number of mbar within it (this overpressure prevents explosive gas mixtures from entering the enclosure). The overpressure is constantly maintained and monitored by the control unit that the customer is using. Inert gas is supplied via a digital valve on the enclosure. If the pressure falls below the set threshold value, the air inlet valve is opened to compensate the pressure loss. If the pressure value measured is still below the threshold value, then depending on which Ex zone it has been defined, either the system will shut down immediately (Zone 1) or the operator will be alerted at least once (Zone 2). The volume of inert gas required for flushing the control cabinet as described above, is a multiple of the cabinet volume and is measured and documented using a measuring method described in DIN EN 60079-2.
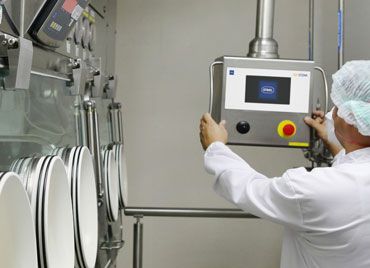
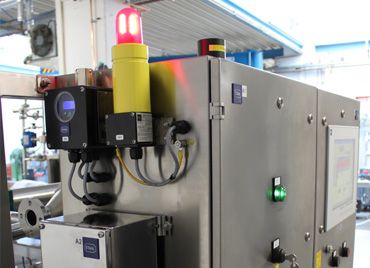
Further advantages of Ex p type of protection for this application are the reduced weight compared to flameproof enclosures (Ex d) and the option to use a vortex cooler to further improve the dissipation of energy lost as heat.
The system operates semi-automatically – user input is via a touch screen produced by R. STAHL, which is integrated directly into the switch cabinet. The interior of these HMI-series devices is designed such that they can be used in pressurised enclosures for Ex Zone 1 and Ex Zone 2 without additional protection measures. The touch screen retains full functionality at all times. The adjustable operating and alert parameters can be entered directly via the screen. The control system has four different operator authorisation levels to guarantee maximum safety and security.
Uninterrupted power supply
Validatable operating parameter archiving is an important capability, particularly in the pharmaceutical industry, and was one of the customer's requirements. The data (pressure, temperature, flow, fill level) is continuously measured at multiple locations and then stored in a database. To avoid losing this data in the event of a power failure, a power supply that powers at least the panel PC should be connected to safeguard the data that has been collected.
This power supply cannot be integrated into the cabinet protected by a pressurised enclosure, since batteries of the required capacity must not be fitted in Ex p or Ex d enclosures. This makes specially approved battery enclosures necessary. Using a modular range of uninterrupted power supplies, R. STAHL devised a suitable solution for hazardous environments. During normal operation in Ex atmospheres, the required batteries are charged to ensure that they can deliver power to the panel PC for a period of approximately 60 minutes in the event of a power failure. An integrated Ex UPS guard, checks if the charger and batteries are functioning properly in accordance with both ATEX directives and IEC/EN 60079 ff, thereby ensuring that they operate safely.
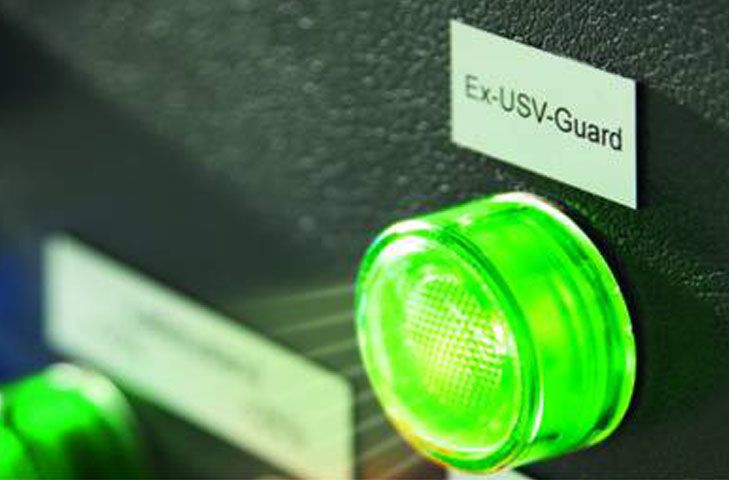