The task: CCTV monitoring for loading/unloading potentially explosive dangerous goods at the berth
R. STAHL was commissioned by a major chemical producer with its own port facility to replace its outdated video surveillance system with a modern one. In the past, the loading/unloading process was monitored from two remote control rooms located farther apart from each other. The outdated analogue video surveillance system meant that the manufacturer could no longer guarantee to provide spare parts, which posed a major safety risk. Re-introducing the so-called “hose monitoring“, i.e. during the loading/unloading process, the tanker is attended by personnel, would have meant a step back, and would have entailed other problems and costs. The solution was a new video management system with state-of-the-art industrial IT cameras for hazardous areas, and high-quality video performance with the best resolution available in the control rooms for accurate decision-making. The monitor equipment in the control rooms was also in need of an update. In general, shifting cargo or an excessively hard collision with the moorings by a tanker containing dangerous goods represents an explosion risk that must be prevented. When a vessel approaches the port facility, everyone needs to be on high alert.
What are dangerous goods?
But what exactly are “dangerous goods“, and what kind of special handling do they require? Cargo is classified as dangerous goods if it contains any substance or material that is capable of posing a RISK to health, safety, property, and the environment during transport. Dangerous goods are classified based on the product’s specific chemical and physical properties: solid,
liquid or gas. The transport of dangerous goods by waterways is governed in Germany by the Dangerous Goods Regulation (GGVSee), in Europe by the ADN (European Agreement concerning the International Carriage of Dangerous Goods by Inland Waterways), and internationally by the IMDG Code (International Maritime Dangerous Goods Code). The Dangerous Goods Regulation (GGVSee) specifies as dangerous goods all those materials and substances that fall under the IMDG Code‘s definition of dangerous goods, as well as certain materials
transported on bulk cargo vessels or tankers. The person responsible for the proper storage of dangerous goods on board ship is the ship operator. He has the best knowledge of the appropriate areas and decides where to correctly store the dangerous goods on board the vessel. CAUTION HAZARDOUS MATERIALS
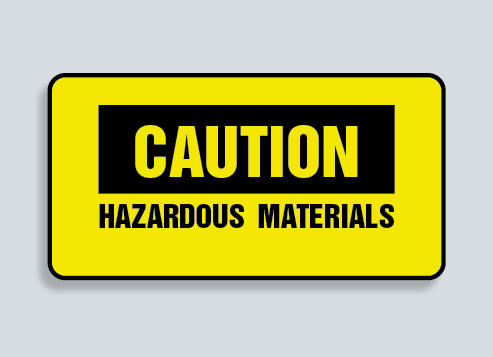
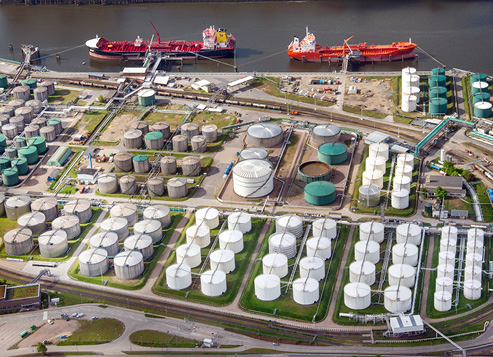
The different steps to deploy the CCTV system
The chemical company uses the dangerous petrochemical goods for further processing. The dangerous goods are transported by ship to the berths, unloaded, and go to storage tanks where they are temporarily stored, before they are further processed in the petrochemical plants. During the loading/unloading of dangerous goods, the point of loading (loading arm / connection to ship) must be continuously monitored from both sides, shipside as well as landside. A new video management system with state-of-theart camera technology on site ensures the required landside monitoring of all operations. The highly sensitive camera modules provide detailed images of the loading process, and, with the support of the control room, enable staff to intervene and stop all operations immediately should dangerous situations such as leaks arise. In addition, the video management system has to be designed to allow for constant expansion or scalability. Two control rooms several hundred meters apart show monitoring images in best full HD image quality thanks to state-of-the-art data transmission. The entire CCTV system has a scalable design, its modules can be easily replaced when required, to keep up with technical progress.
STEP 1: Site inspection
For this project, we carried out a site inspection at the port facility in order to include all conditions on site in the system design. Some of the many issues distance between control room and area to be monitored, the use of existing cameras or existing cabling, the use of monitors in hazardous areas on site, task-specific requirements the cameras have to fulfil, etc.
STEP 2: System design and configuration
The results of this site inspection are integrated into the system design, as the basis of all considerations concerning the best possible system solution. In close cooperation with the customer, we discuss the advantages and disadvantages of various possible solutions. The final option is then submitted to the responsible parties for the go-ahead, followed by the actual realisation, starting with the configuration.
STEP 3: System test and integration
We compile the complete CCTV solution in house and submit it to rigorous testing. Potential breakdowns are simulated, and the system is tested under extreme conditions. After successfully passing the tests, the CCTV system is ready to be integrated into the customer‘s facility.
STEP 4: FAT, SAT and commissioning
A handover of the “turnkey“ system to the customer takes place either in house at R. STAHL as a FAT (Factory Acceptance Test) or directly on-site as a SAT (Site Acceptance Test). The customer can fully examine how the system works and how the individual materials are used. R. STAHL is a trusted supplier of high-quality goods and services, and we are more than happy to carry out these acceptance tests. After approval by the customer, the complete CCTV system is delivered, installed and commissioned at the customer’s site.
STEP 5: Training and documentation
Although often underestimated, TRAINING AND DOCUMENTATION are extremely important. An individually tailored training program for the customer’s staff familiarises them with everything the new CCTV system has to offer. In addition to instructions on how to operate the cameras and servers, particular emphasis is placed on familiarisation with the software, i.e. the video management system. In addition to the state-of-the-art software, intelligent cameras with analysis functions feature many monitoring options, with the majority being customisable to meet the requirements of individual applications.
STEP 6: Service and maintenance
Last but not least we offer individual service and maintenance plans. We prefer individually tailored plans since every system has different requirements and is subject to different demands. Most important is that the CCTV system is in constant, full operation, and we make sure this is the case.
R. STAHL uses its wide range of explosion-protected and industrial cameras
R. STAHL uses its wide range of explosion-protected and industrial cameras together with servers, switches, and any other required accessories to develop the ideal CCTV system for each individual application. Also of importance is that the surveillance systems can always be expanded or extended. The electropolished stainless-steel enclosures (316L, 1.4404) of the EC-PTZ cameras are designed for reliable long-term operation and, thanks to their Lloyd’s certificate, they are suitable for maritime applications. Certified according to ATEX, IECEx, NEC, CEC, EAC and LR, all cameras can be used world-wide. In addition, all R. STAHL cameras feature the internationally recognised ONVIF standard – a global, open industry forum with the goal of facilitating the development and use of a global, open standard for the interface of physical, IP-based security products.
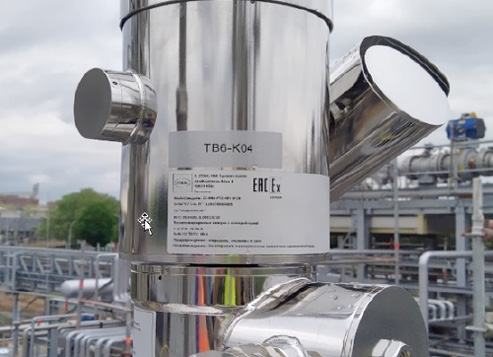
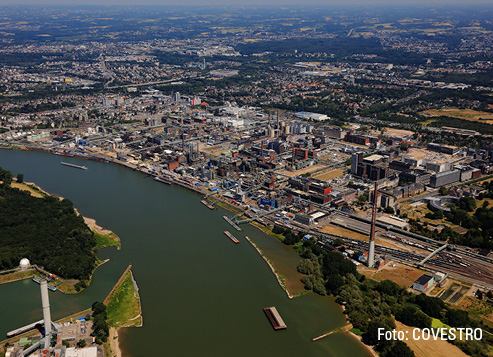
Application-specific CCTV systems in hazardous areas
Application-specific CCTV systems in hazardous areas drastically speed up and simplify any necessary process intervention, thereby substantially improving safety. There will be a quick return on investment for a CCTV system at this port facility, because elaborate and costly guard tours by staff working a relatively long distance away in the control rooms are no longer necessary. In addition, a CCTV system ensures increased safety because it can simultaneously monitor several critical points during the berthing of a ship.