R. STAHL and LUVRA ensure safety and operation of LNG loading arms
Loading arms for LNG are almost as unique as a fingerprint. No two are exactly the same. LUVRA Hydraulik and R. STAHL work together to ensure that these crane-like structures can move and are safe to operate. LUVRA is responsible for planning the industrial hydraulic system, including the electrical engineering. Following this, R. STAHL constructs the explosion-protected electrical control systems – tailored to each individual project. The two companies have learned a lot from one another over the course of their 25-year collaboration. Together they have created solutions that benefit LUVRA, loading arm manufacturers and especially the users who then go on to operate these products.
Tailor-made for special machine construction
Liquefied natural gas is currently on trend. In actual fact, LNG (liquefied natural gas) has been transported across oceans for many years now to places without a natural gas pipeline or without a sufficient natural gas supply from a pipeline. LUVRA Hydraulik und Regeltechnik in Nuremberg supplies an essential technical component for the LNG industry – electrohydraulic control systems for the loading arms. Their functions include loading or unloading ships. A standard solution is seldom suitable here. In particular, large loading arm manufacturers with expertise in transshipping hazardous materials like LNG develop loading systems specifically tailored to each individual application. This is also true of the combination of an electrical and hydraulic control system supplied by LUVRA.
Stefan Hahn is LUVRA's electrical engineering expert. Since 2002, he has been working on project engineering for electrohydraulic control systems for LNG, oil, gaseous media and other media. "The electrohydraulic system parts that we construct are often also used in hazardous areas," explains Hahn. The first time the company received a request for a loader suitable for LNG, in other words one that can operate at temperatures of -170 °C, this proved to be a challenge.
Smooth-running loading arm in the float position
When it comes to the electrohydraulic technology for these LNG loading arms, nobody knows it better than Stefan Hahn. Over the last 20 years, he has managed around 13 projects involving more than 50 loading arms – from project engineering through to programming the control system and commissioning. At a later stage, the hydraulic system has to ensure that the loading arm compensates for the movements of the LNG tanker that is being unloaded. This is because, even when the weather is calm, a ship is constantly in motion due to the swell. Hahn explains: "As soon as the loader is connected, it moves to the float position. If the arm moves, the cylinders of the hydraulic unit are pushed in or out. One person could move this arm by themselves, as it's extremely smooth-running." The solution from LUVRA therefore doesn't just have to work on its own. It is designed to interact with the systems from LNG loading arm suppliers, which control movements of the LNG loading arm but also transmit status messages and errors. In an emergency, the loading arm must separate from the ship automatically. It must also be ensured that as little LNG as possible escapes.
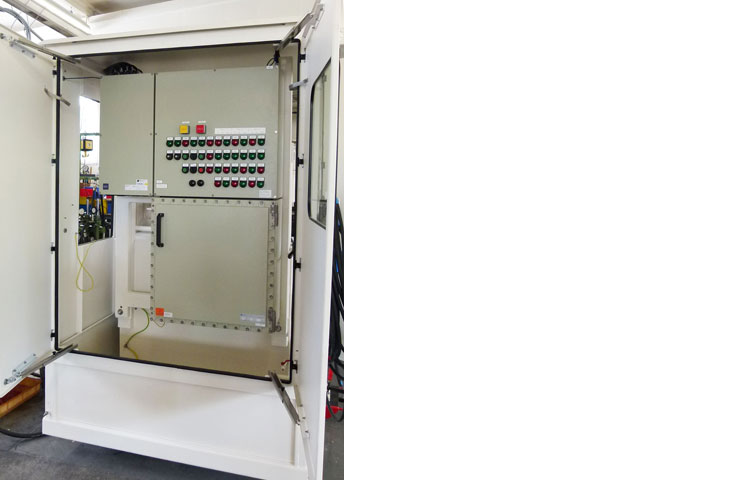
Expert knowledge of explosion protection for international projects
It therefore comes as no surprise that the safety-relevant equipment not only includes explosion-protected control technology but audible and visual alarm systems as well. For decades, R. STAHL from Waldenburg has supported the experts at LUVRA with these products – and with a wealth of knowledge. This is because LUVRA must adhere to differing explosion protection regulations. In Europe, the ATEX directive applies - in the international area IECEx (for example in Australia). In addition, different regulations apply, for example in Canada, the USA or Korea. Hahn references the Chinese market, where the China Compulsory Certification (CCC) has been required since 2020. R. STAHL can ensure all of this for operating and monitoring systems, control systems and distributions, signalling devices, automation systems, luminaires and many other components. Stefan Hahn also regularly obtains detailed knowledge from his partners at R. STAHL, no matter whether this concerns hazardous area regulations in China or Korea or the suitability of operating or signalling devices for particularly harsh conditions, for example in extreme outside temperatures. Hahn praises the fact that "the specialists at R. STAHL have always been extremely knowledgeable and skilled points of contact."
Minimising hazards, even in the event of operating errors
Explosion protection must still be effective even if an operating error causes large quantities of LNG to escape. Hahn mentions an incident which occurred in 2000, when an operator of a system in Pakistan accidentally triggered a manual EMERGENCY STOP. "The loading arm with 12-inch pipes shot backwards like a rocket and a huge quantity of LNG escaped. Even in a case like this, the hydraulic system must prevent damage to the system, while the electrical system must prevent an explosion." Needless to say, this also applies to an emergency separation initiated by the control system, for example if the ship moves excessively or the LNG tanker drifts away from the unloading terminal. In this case, an emergency breakaway coupling largely prevents damage and LNG leaks.
Increasing demand for ship-to-FSRU loading
Loading arms also make ship-to-ship loading possible, whereby one of the ships is used as the regasification unit and is securely anchored in port for the majority of the time. LUVRA has implemented this configuration in Brazil, Argentina, Kuwait and Pakistan, among other countries. FSRUs (floating storage and regasification units) are also planned for Germany's first LNG terminals in Wilhelmshaven and Brunsbüttel. Other projects are currently underway in Finland and Estonia.
Flooding on the Mississippi – the enclosure is tight
When starting a new project, Hahn always collects some information first. Details about the future site are important, not least the Ex protection regulations that apply there. The outside temperatures, as well as any earthquake or flood risks, are also relevant to the design of the hydraulic system. Hahn recalls how "two of our units on the Mississippi were completely flooded. We had to drain the entire hydraulic system, then clean and recommission it – involving huge expenditure. If we had known about the flood risk, we would have positioned the hydraulic system on a platform." The entire electrical control system was actually underwater. But the enclosure from R. STAHL remained tight. The list of general conditions that the LUVRA project engineers wanted information about is much longer still – and meeting this request is very important to Hahn. The R. STAHL engineers are also interested in many of these details. R. STAHL Sales Manager Christian Pflugfelder knows that "when choosing our electrical components, the ambient temperatures at the installation site also play a major role, as these are important for calculating the power dissipation correctly."
Reliability and redundancy in the face of failure costing millions
The compactness of the control system that R. STAHL achieves using Ex d enclosures is especially important for LNG loading devices in particular. Sensors that the loading arm manufacturer uses for monitoring purposes often also have to be integrated. LUVRA ensures that the intrinsic safety of the entire electrical circuits is proven. Just like the hydraulic system, the electrical system also has to be robust, reliable and durable. Redundancy in many functions ensures that the unloading station never fails. For example, a wired control unit has been added to the radio control system in order to prevent total failure in case of error. "For each day that a customer is unable to load LNG", which Hahn describes as the worst-case scenario for them, "50 million euros are at stake."
R. STAHL not only provides expert advice about explosion protection issues and expert products; the company based in Waldenburg is also responsible for building the Ex d control systems, based on the electrical diagrams by Stefan Hahn. The IS1+ remote I/O system is often used for larger projects. Pflugfelder explains: "This allows us to easily combine many signals. LUVRA also has the freedom to use the exact third-party control systems that the end customer would like." Every project includes additional equipment such as signal horns and flashing beacons from R. STAHL. In the end, every control system looks different, including when it comes to the number of actuators and sensors that are used in the individual project. Even just three loaders entail many valves, motors and sensors. If redundancy is also required, the scale can turn out to be massive. "In this case, we attempt to position the solution in the non-hazardous area if this wouldn't make the cables too long," reports Hahn. However, there was already a control system on a support, four metres long and two metres high, made from Ex d enclosures joined together.
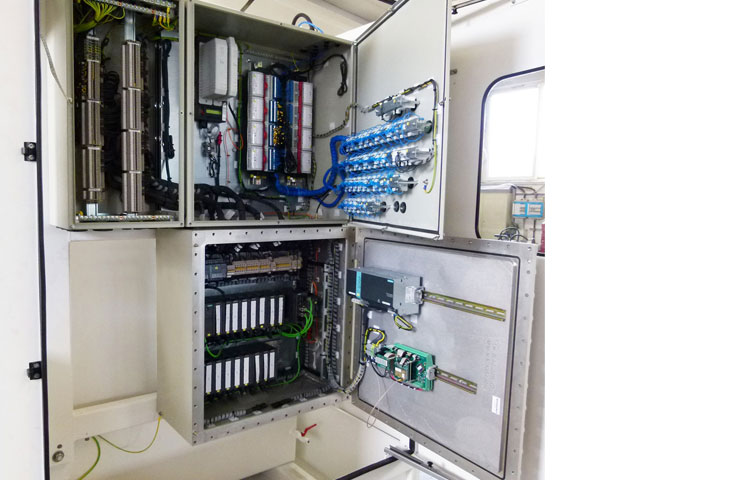
Fruitful collaboration between partners
The customer-supplier relationship that LUVRA and R. STAHL have maintained for 25 years has already given rise to a wide range of different solutions. "The collaboration was always very constructive. The engineering experts at R. STAHL are very knowledgeable and skilled. And they always explored any suggestions for optimisation that I had," recalls Hahn. This is how the collaboration between these two partners created a "standard solution" as the basis for up to 80 per cent of all LUVRA systems, among other developments. "Make it simple" was the motto. This motto in no way contradicts LUVRA's claim to always develop the perfect electrohydraulic solution for each individual project. Hahn praises the optimisation of the wiring, as for some time now he has been enjoying the benefits of installed parts that are easy to snap into place on the front. The momentum that the LNG industry was recently given is certain to yield additional solutions and further consolidate the good customer-supplier relationship between LUVRA and R. STAHL.