R. STAHL digitalises the lighting in Ex Zone 1 for Sika
With the ban on fluorescent tube lights in the EU, many companies which operate industrial plants are considering alternative lighting systems. Alongside a simple replacement with LED light fittings, retrofitting also offers the opportunity to create added value through digitalisation. R. STAHL has played a pioneering role in a project for Sika Deutschland GmbH and designed a modern digital lighting solution for Ex Zone 1.
Health and safety
You don't need to be a technology nerd to find the view of a refinery or chemical plant at night beautiful. Illuminated by dazzling light, the industrial complexes attract attention even from afar. But there's a reason why the lights are on day and night: To keep the people working there safe. However, this comes at a price – starting with energy costs, power consumption and the associated carbon dioxide emissions. The dark side of continuous lighting affects nature conservation too – just think of the insects which are drawn to lamps.
This is why combining health and safety in the workplace with sustainability while making building technology future-proof was high on the list of priorities for a project run by construction chemical specialist Sika. With more than 33,000 members of staff and 400 factories in 103 countries, the Swiss company is a global player in the market for construction chemical products, for example sealants and adhesives. Sika's sustainability strategy is summed up by the principle "More value, less impact", and part of this is continuously reducing the consumption of resources.
At the German manufacturing site in Kornwestheim, the company has now entered uncharted territory: A fully digital lighting solution has for the first time been used in two production and storage areas classified as Ex Zone 1. This allows the lighting to be precisely tailored to on-site requirements. This not only saves electricity and reduces maintenance requirements, it also makes it possible to inspect and document emergency lighting in line with legal regulations. But first things first.
Benefits of using modern LED technology
There are many reasons to replace conventional lighting systems with modern LED technology – these include the EU's ban on common T5 and especially T8 fluorescent tube lights, which came into force in August 2023. From this point on, retailers in the EU have only been able to sell off their remaining stock. Although the ban does not apply to light sources used in hazardous areas, it is likely that the range of available lamps for this application will become far smaller.
While the investment costs for LED lighting systems are usually higher than for conventional fluorescent lamps, it's not usually these costs that have the greatest influence on the overall balance sheet in industrial plants. Instead, it's the operating costs, especially the power consumption and maintenance requirements, that are the most significant. LED lighting is clearly superior here as the initial costs are recouped relatively quickly: Replacing fluorescent tubular lights with LED light fittings halves the energy consumption according to estimates by ZVEI, a German manufacturer's association. Savings of up to 70% can be made if the LED light fitting is also controlled depending on the available daylight or the presence of operating personnel (presence control). Having the lighting system designed by professionals can achieve further energy savings of 10%.
While it sounds like there are already enough convincing reasons to make the switch, it makes even more sense for industrial areas and, in particular hazardous areas in the (petro)chemical industry. The reason? Maintenance costs represent a huge expense here in the long term. The service life of fluorescent lamps is only one quarter to one fifth of the service life of comparable LED light fittings, while their luminous intensity noticeably decreases during this period. In plants in the process industry, replacing lamps, particularly in hazardous areas, is a time-consuming and complex process. Fewer maintenance cycles for LED light fittings with a service life of between 50,000 and 100,000 hours mean huge cost savings for operating companies. This is because a risk assessment has to be drawn up and appropriate protective measures taken each time a maintenance task is performed in a hazardous area. What's more, only specially qualified staff are permitted to plan and carry out work in hazardous areas – otherwise there could be liability issues and the safety of the products will no longer guaranteed.
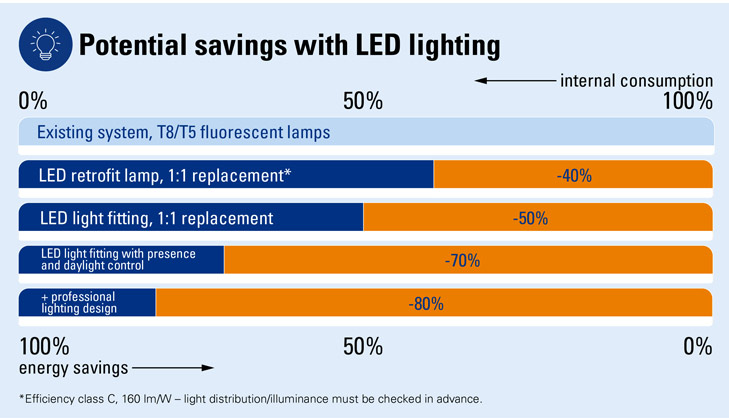
Testing of emergency luminaires automated
And that's not all – self-contained emergency luminaires used to illuminate escape routes in the event of a power failure in this area with particular requirements have to be inspected on a regular basis. DIN EN IEC 60079-17 (Electrical installations inspection and maintenance) stipulates a weekly visual inspection of the central power supply and for battery-based systems – whether self-contained or with a central battery – weekly testing, as a minimum, with the secondary voltage source connected. To do so, the line voltage is disconnected, which activates the battery-based power supply. Then every single luminaire is tested individually. Although it is relatively easy to conduct the requisite weekly tests on self-contained emergency luminaires, it does take a bit of time: It requires on-site plant personnel to manually initiate a self-test or, for luminaires with an automatic self-test function, to check the status of a status LED on the luminaire and record it in the test/inspection log book.
This is why, for Sika, it was clear from the outset that new lighting system, intended for two buildings with four rooms and over two floors (Ex Zone 1) shouldn't just be retrofitted but also digitalised and integrated into the building management system. The reason? Sika already uses modern light management concepts in non-hazardous areas. For the project in hazardous areas, Sika got in touch with the lighting experts at R. STAHL, which specialises in providing explosion protection and automation solutions. After a tour round the site, the specialists carried out the calculations for the lighting and then created a tailored lighting solution. This was necessary because the request to integrate the LED light fittings in hazardous areas into the central building management technology based on the KNX standard called for a custom solution. The KNX Konnex bus has already been used for automation applications in conventional building technology for some time now. KNX makes it possible, for instance, to intelligently link heating, lighting, blinds, ventilation and building security technology.
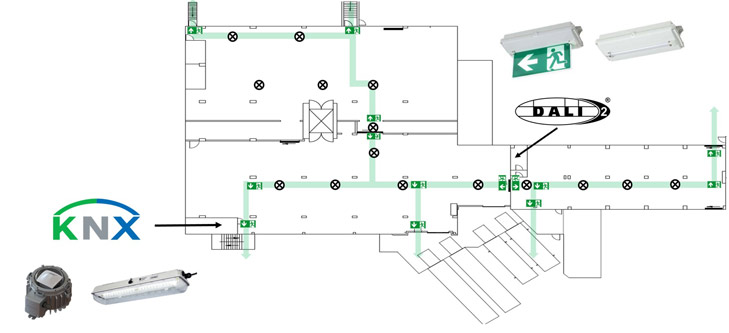
DALI system integrated into the building management system based on KNX
For digitising the lighting systems in hazardous areas, R. STAHL uses the DALI2 digital addressable lighting interface, which is standardised in accordance with IEC 62386. This system, developed specifically for lighting technology, makes it possible to control luminaires individually. R. STAHL's linear luminaires and emergency luminaires have a DALI2 interface, meaning that consistently modern, flexible and energy-efficient light management can be implemented even in hazardous areas. And DALI makes it possible to automate weekly inspections of self-contained emergency luminaires and escape route luminaires through continuous electronic monitoring of the luminaires. DALI allows for bidirectional communication between the central DALI system and the bus nodes. As a result, not only can the luminaires receive commands, they can also send status information back to the control system. This replaces inspections and makes it possible to define maintenance cycles individually for each luminaire. This means that maintenance can be planned and carried out automatically. This is important because emergency repairs are expensive in industrial areas and especially in hazardous areas. To get the best of both worlds – the building system technology and general lighting – R. STAHL has developed an interface concept which links DALI to the higher-level KNX system.
Specifically, the DALI luminaires from the general lighting can be incorporated into a KNX control system via a KNX gateway. The KNX gateway converts the DALI signals into KNX commands, enabling the lighting to be switched individually and synchronously. Different lighting levels and dimming behaviour for LEDs can be defined for every luminaire and luminaire group. Using time control and via connected presence and daylight sensors which have been developed for use in hazardous areas, the light intensity is automatically adjusted to the operational processes and ambient brightness. Having these fully lit during the day in case of gloomy weather conditions, which used to be standard practice in many plants, is now a thing of the past. This significantly extends the service life of the luminaires. Furthermore, switching states, error messages and brightness values can be automatically retrieved via DALI communication. This makes modern preventive maintenance concepts possible so that failures can be minimised.
The luminaires as part of Sika's safety and escape route lighting are operated via two separate DALI central units, thereby simplifying maintenance. The planners adapt the light management infrastructure to the on-site conditions.
R. STAHL completed the entire project at Sika within a year and the new lighting system was commissioned. The custom lighting concept now not only ensures that the illumination of work areas looks good, meets requirements and functions well, but also achieves significant energy savings. Based on an automated test of the emergency lighting at the weekend, the operating team receive a test report at the start of their shift on Monday and can plan maintenance measures if required. And the digitalised lighting solution is future-proof: It allows new requirements to be implemented – for example in the event that future regulations should call for presence- or daylight-dependent lighting. It holds true that the future is digital – now for hazardous areas too.
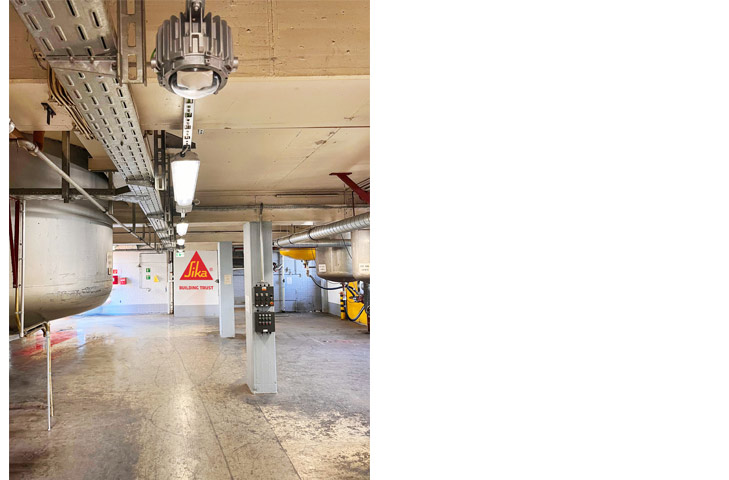