How URACA is making processes clean and stable with modular HMI systems
Regular high-pressure cleaning of reactor containers not only ensures a clean process, it also helps to optimise production times and make complex processes stable. URACA's high-pressure cleaning solutions can be used to clean even sophisticated and hard-to-reach geometries without leaving any residue behind. This means that the necessary HMI systems are subject to stringent requirements – as the processes have to be reliably monitored, operated and controlled. URACA opted for an HMI system from R. STAHL's new modular ORCA device platform for a recent project.
Pump systems have to be powerful and reliable
Interior cleaning of containers covers a wide range of applications. The cleaning system to be used always depends on the type of dirt to be removed. A new project from URACA concerns an automatic reactor cleaning system with pneumatic drive. This system is implemented in Zone 1 IIB T4 hazardous areas. It is composed of six cleaning lance systems, each consisting of two lances. The aim is to use the two lances, which operate simultaneously, to clean six reactors, each of which is up to approx. seven metres tall and has a diameter of around four metres.
Two RS724 EEx/400, Zone 2 IIB T4 high-pressure pump systems are connected to each lance. These RS724 high-pressure pumps from URACA boast an operating pressure of 400 bar and a flow rate of 209 l/min. They can be described as robust displacement pumps. The sophisticated design of the pump results in low energy consumption thanks to high mechanical efficiency paired with low-wear operation. Each of these high-pressure pumps in this recent projects supplies six cleaning lance systems. In the event of a pump system inspection, the pumps can be switched over using a monitored crossover hand valve. This ensures that the second pump can be used for cleaning without any interruptions. The cleaning system is powered by a frequency-controlled 160 kW 380 V 50 Hz 1500 rpm three-phase asynchronous motor for II 2G Ex de IIB T4 hazardous areas.
An URACA tank cleaning head (TWK), which can be used in hazardous areas up to Zone 0, is fitted to the end of the lance. This tank cleaning head has a rotor which is used for cleaning with a jet of water and recoil forces. A monitored locking unit keeps the lance in the park position. The combined and monitored high-pressure double pneumatic switching valve (DPSV) activates or deactivates the high pressure at the tank cleaning head nozzles and the low pressure at the spray ring. The lance positions can be set precisely to meet individual requirements and adapted to achieve the very best cleaning results. This process is supported by an encoder. This makes it possible to automatically move to up to ten previously configured positions in any selected order.
The automation and drive system includes a control and drive unit and an operating and monitoring panel (HMI), which is used to operate, monitor and control the entire cleaning and pump system. The drive unit consists of a power cabinet with a frequency converter, which is positioned in the air-conditioned motor control centre (MCC) provided by the customer. The Profinet interface is used to communicate with the Siemens S7-1500 controller. In an emergency, the frequency converter will be switched off safety related manner. The control unit consists of a control cabinet with the Siemens S7-1500 fail-safe controller and other monitoring, switchgear, safety and explosion protection equipment. The control cabinet is positioned in the air-conditioned control room. Fibre optics are used for transmission due to the conductor length of 500 metres.
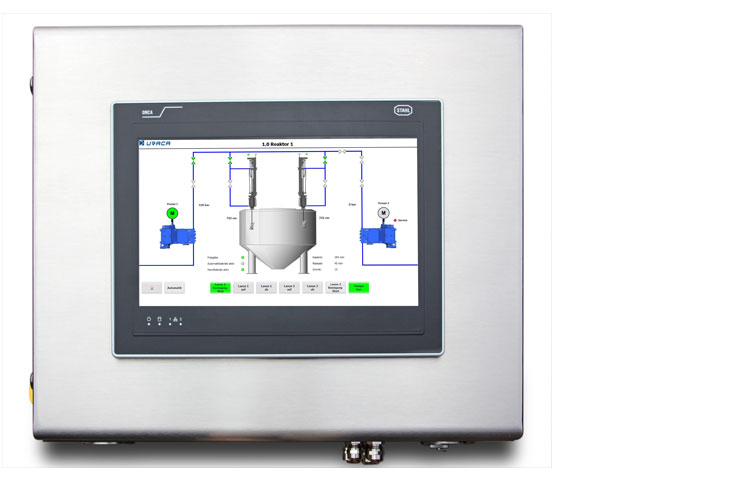
The modular concept makes the HMI system sustainable
The HMI panel PC, which is certified in line with ATEX/IECEx, NEC and CCC China Ex, reliably monitors, operates and controls the entire high-pressure cleaning system in the reactor cleaning area itself. The panel PC used is a 15" device from R. STAHL's new modular ORCA device platform. R. STAHL's modular approach for the HMIs is new: Individual components of the ORCA devices, such as the electronics box or the display box, can be replaced separately. This is of particular advantage in terms of sustainability and future-proof investment. Unlike encapsulated devices which have to be returned to the manufacturer for repair, the modular ORCA devices can be replaced by the operator's staff themselves. Machine manufacturers can use the modular design to provide their customers with a fully preconfigured computing unit in the case of hardware updates or repairs. This saves time and money. This updatability guarantees a future-proof investment for a minimum of 15 years. "The new EasyConnect concept of the ORCA device platform won us over straight away. The display and electronics module can be separated in a few easy steps. The old electronics box is replaced with a new, more powerful one. This modularity makes the ORCA an HMI concept which will be able to keep pace with future technological advancements," reports Harald Claß, Head of Electrical Design at URACA.
The reactor cleaning system has a built-in 15" panel mount device. The ORCA device platform comes in 12", 15" and 22" variants and the devices are suitable for Ex Zones 1, 2, 21 and 22 as well as Classes I and II, Division 2 and Class III. Of?modular design, they consist of an electronics box and a display box, making them scaleable to suit your needs. Displays and touchscreens are protected by a front of hardened glass, making the devices considerably more robust than conventional resistive touchscreens. All three device sizes boast bright and high-contrast wide-screen displays and have full IP66 protection.
The visualisation based on S7 SIMATIC Win CC gives the user a complete overview of the system, enables them to select the different reactors via menu windows, control and monitor cleaning sequences with one or two lance systems manually or fully automatically, and parametrise and select programs. Status and error messages and information on the pump and high-pressure operating hours indicate the current status of the system. It is also possible to switch to the country-specific language.
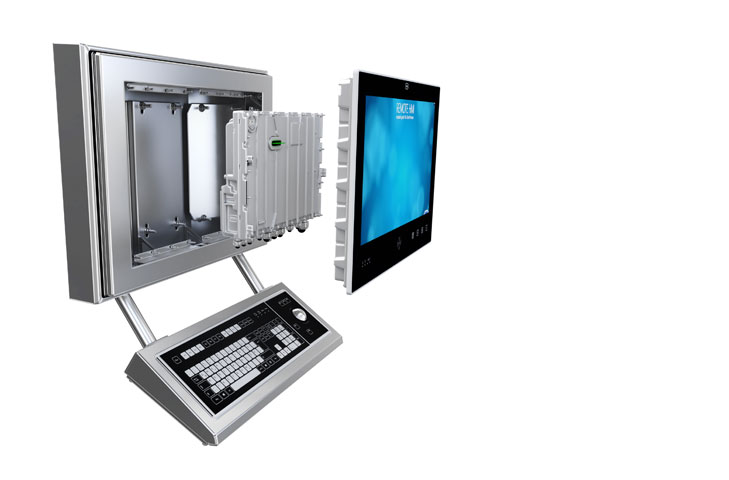
Conclusion
The HMI systems of high-pressure cleaning solutions are subject to stringent requirements. It's good that URACA can rely on the components used, worldwide certificates, explosion protection and service aspects of R. STAHL's new ORCA operating devices.