How mobile spectrometers help optimise pharmaceutical production
Spectrometers are being increasingly used in pharmaceutical production, for purposes including process monitoring. But conditions in production are more stringent than in laboratories. To be able to use a laboratory device in hazardous areas too, R. STAHL has installed an NIR spectrometer in a specially developed control cabinet for a leading pharmaceutical manufacturer. And to top it all off: The premium spectrometer is now mobile, so it can be used at different locations.
Intoduction
Taking samples, transporting them to a laboratory, analysing them and adapting process conditions – this procedure is standard in the production of active pharmaceutical ingredients. But a lot of time passes before the results of a laboratory analysis are available and the production team can react to these. Often the opportunity is missed to control the reaction that is happening and to save the batch. To get an insight into the process, manufacturers in the chemical and pharmaceutical industry therefore want analytical devices that can be used to monitor the reaction process and the product quality online while the production process is ongoing. But this means that the devices have to meet completely different requirements compared to operation in a laboratory. The reason? In the production process, not only could the ambient conditions interfere with the sensitive analytical devices, the production areas are also often classified as Ex zones due to combustible dust or the use of combustible solvents. Electrical devices used there must be specially designed to prevent them turning into a source of ignition. Process analytical devices designed and built for such environments are rare and usually also expensive.
Real-time monitoring in hazardous areas
R. STAHL's pharmaceutical customer already had an NIR spectrometer in their laboratory. But the customer wanted to use this expensive device flexibly in their production process too, and not just in the laboratory. Ultimately the aim was to optimise the production process using quick and precise NIR spectrometry and to guarantee the quality of the medicines. Since the pharmaceutical producer had previously called on R. STAHL's expertise in producing customer-specific control cabinets, particularly in explosion-protected areas, the Waldenburg-based manufacturer was the obvious choice when it came to finding a solution in this application too.
The acronym "NIR" stands for "near infrared" – a spectroscopic analytical process which analyses the chemical composition of materials using infrared radiation. This method involves radiating infrared light with wavelengths in the range from 780 to 3000 nanometers on to a sample. The way in which the molecules of the material absorb or reflect this light provides information about its structure. This process is non-invasive and fast, and makes accurate quality checks possible, for example to check the ingredients of foodstuffs or medicines without damaging the samples.
The team at R. STAHL was tasked with integrating an NIR spectrometer into a mobile, explosion-protected control cabinet in order to monitor the quality of tablet formulations flexibly and in real time. This was challenging for technical reasons as the spectrometer had to be both mobile and explosion-protected. The critical factor for the pharmaceutical company was the monitoring of the quality of the tablet formulations during the granulation process – an important step in producing tablets. Since many of the chemicals and solvents used can create an explosive atmosphere, explosion protection was one of the fundamental requirements of the project.
Two options: Stationary or mobile?
There are essentially two approaches for integrating the NIR spectrometer into the production process. One option was to install the spectrometer outside the hazardous area and route the explosion-protection sensors into the production area. However, this solution would have required really long glass fibre-optic sensors of up to 40 metres, which would not only have been impractical, but also expensive and prone to faults.
The better alternative was to integrate the entire spectrometer into the hazardous area. This is where R. STAHL came into the picture: The specialists in automation and explosion protection suggested that the best solution in terms of technology and cost-efficiency would be to house the spectrometer in an Ex p control cabinet. "Ex p" stands for "pressurised enclosure" and is a method for protecting electrical equipment used in hazardous areas. With Ex p, a higher pressure is maintained at all times inside the control cabinet compared to the surrounding atmosphere. This prevents explosive gases or dust entering the enclosure and becoming sources of ignition. Prior to commissioning, the enclosure is first purged with instrument air or inert gas to remove all hazardous substances. The purge air volume used for this is at least five times the enclosure volume – in the current application, purging is performed for 30 minutes. If the excess pressure drops during operation, a monitoring system switches off the installed device and triggers an alarm. This degree of protection is perfect for the pharmaceutical manufacturer's NIR spectrometer as it not only guarantees explosion protection, but also protects the sensitive device against dust and aggressive media which could be present in the production environment.
Mobility and flexibility: One device, multiple operating locations
One of the main requirements for the project was that the control cabinet had to be mobile. The pharmaceutical producer needed a solution that made it possible to flexibly use the spectrometer at different locations within production. R. STAHL developed a mobile control cabinet on conductive castors which reliably prevent electrostatic charge. Thanks to this mobile solution, the expensive spectrometer can be used in multiple production processes, which dramatically reduces costs. A mechanical mount has been integrated for secure storage of the cables so that the sensitive sensors and cables can be stowed away safely when the spectrometer is not in use.
Technical solutions: HMI and cable management
Another highlight of the project was the integration of a modern HMI (human-machine interface), which has been fitted to a swivel arm on the control cabinet. With the new ORCA series, R. STAHL's range includes an operating device produced in-house which not only meets stringent explosion protection requirements but also has a design suitable for use in the pharmaceutical industry. This way, the operator can monitor the spectrometer directly on-site and control it without being reliant on external systems. The spectrometer's analysis software is also directly integrated into the device and is convenient for the system operator to use. The HMI features safety glass and offers a user-friendly interface for analysing and configuring the parameters of the device. The swivel arm designed specially for this control cabinet solution also incorporates the connection cables for the HMI. By mounting the monitor on the swivel arm, the mobile solution is not top-heavy unlike a cabinet solution with built-in monitor.
Cable management also posed a problem, as the standard cable bushings were not wide enough for the spectrometer's large fibre-optic sensors. R. STAHL solved this problem by using a flexible multi-cable transit (MCT) system, which ensures a safe and gas-tight seal. An Ex plug connector developed by R. STAHL was used for the power supply. Cable glands with strain relief were also fitted to protect the movable cables. Another standout feature is the drawer structure inside the control cabinet. This makes it easier to access the spectrometer when the control cabinet is open.
Maintaining a stable temperature inside the control cabinet was another critical aspect that had to be considered. Temperatures in the production environment can rise quickly, particularly in summer or in warm climate zones. To ensure that the spectrometer operates in optimal conditions, R. STAHL integrated a regulated cooling system which additionally uses the purge air as required to keep the inside temperature stable.
Explosion protection and materials
The control cabinet is made from corrosion-resistant stainless steel in order to meet the strict hygiene requirements in the pharmaceutical industry. All surfaces have been machined so that they are easy to clean and no residues or contaminants adhere to them. This is particularly important because the control cabinet is regularly used in an environment where different chemicals and substances are processed.
To ensure explosion protection, the cabinet has not only been constructed in line with the specifications for the Ex p type of protection, but the design features for the Ex e type of protection have also been incorporated at the same time. This means that, alongside the Ex p system – consisting of control unit, pressure monitor and air intake assembly – additional safety components required, like an Ex e miniature circuit breaker and an Ex e enabling contactor, can also be used as an open assembly inside the control cabinet.
Conclusion: Tailored solution
The project demonstrates the importance of tailored solutions in explosion-protected areas. R. STAHL has developed a mobile Ex p control cabinet which makes it possible for the pharmaceutical company to use an expensive and sensitive NIR spectrometer safely and flexibly in production. By combining mobility, an explosion-protected design and user-friendly operation, R. STAHL was not only able to meet the high safety standards but also to help the pharmaceutical producer boost efficiency in production.
The project was completed on time and to the full satisfaction of the customer. The pharmaceutical company is already planning to use additional mobile Ex p control cabinets for other application areas, which is testament to the successful collaboration and the high quality of the solution.
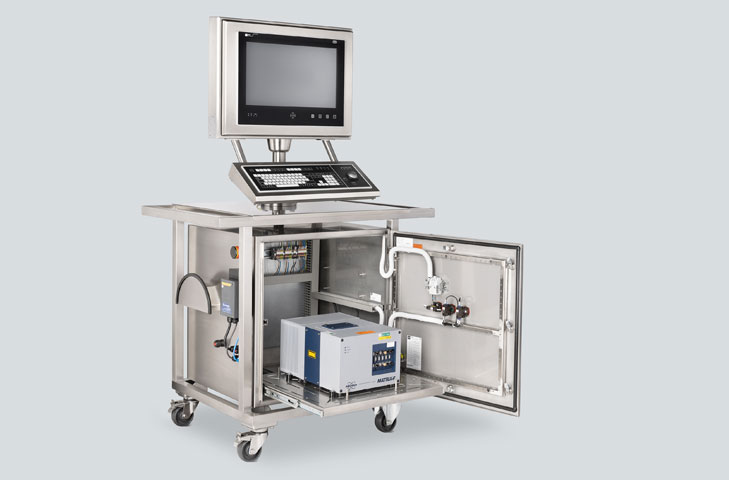